Progress Report: December 2018
December 16, 2018
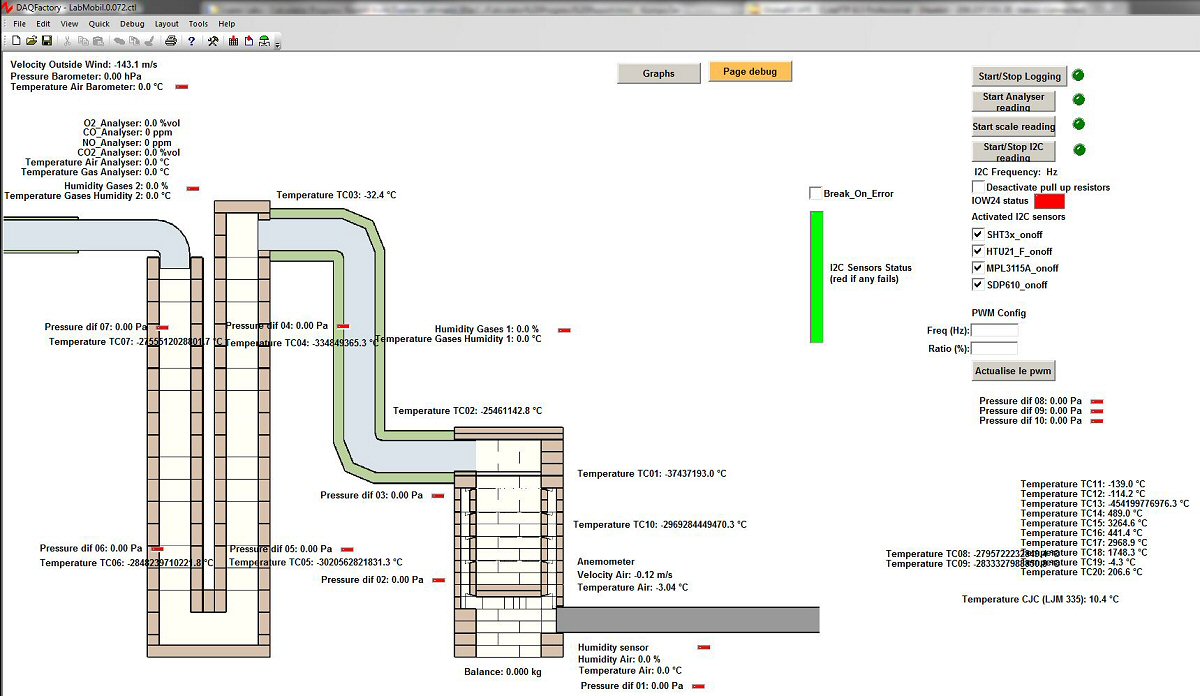
The graphic above is a screen capture from DAQFactory, which is the SCADA (Supervisory control and data acquisition) software that we use at the AFPMA lab and the MHA lab to interface the data acquisition sensors in the test heaters. Setting up the sensors and software has been a year+ long project.
You
can also get an idea about the "heater calculator" project from the
above diagram. Notice that as you go from the combustion air inlet,
through the firebox, the channels, and then into the chimney, you have
a set of pressure and temperature sensors that make a complete circuit from inlet to outlet.
This is the basic idea of the calculator, except in reverse. In the calculator, you input your dimensions, chimney height, etc. The software then predicts what the pressures and temperatures in
the heater/chimney circuit will be, to verify that the sytem will
function properly. For example, that the channels are not too long to provide enough draft, or that the stack temperature is not so high that it will lower efficiency.
In order to proof the calculator, we need to build some actual example heater setups and instrument them, to verify that the software simulation (calculator) provides the correct results.
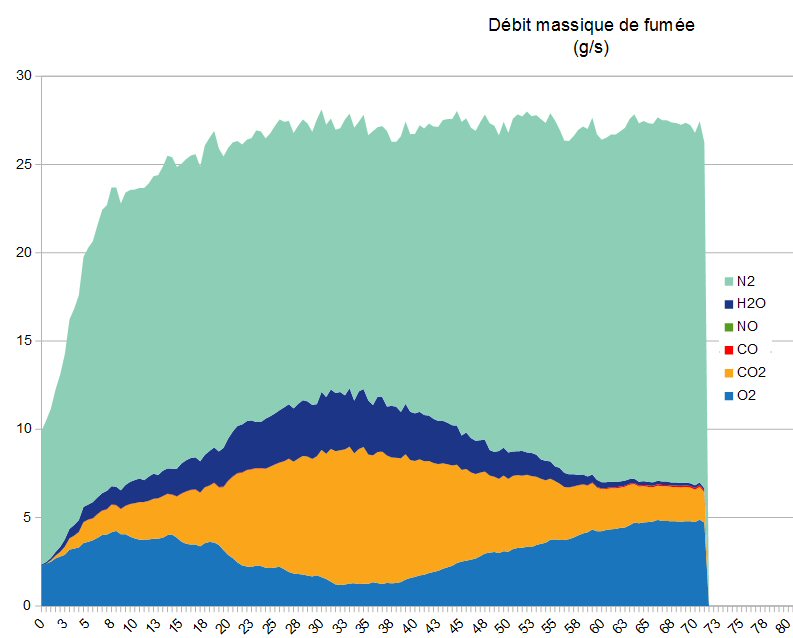 This is an early (Dec 2018) demonstration from the AFPMA lab showing the flue gas mass flow, and the contribution to mass flow from the different flue gas components. Measuring the water mass flow in the flue has been one of the most challenging aspects.
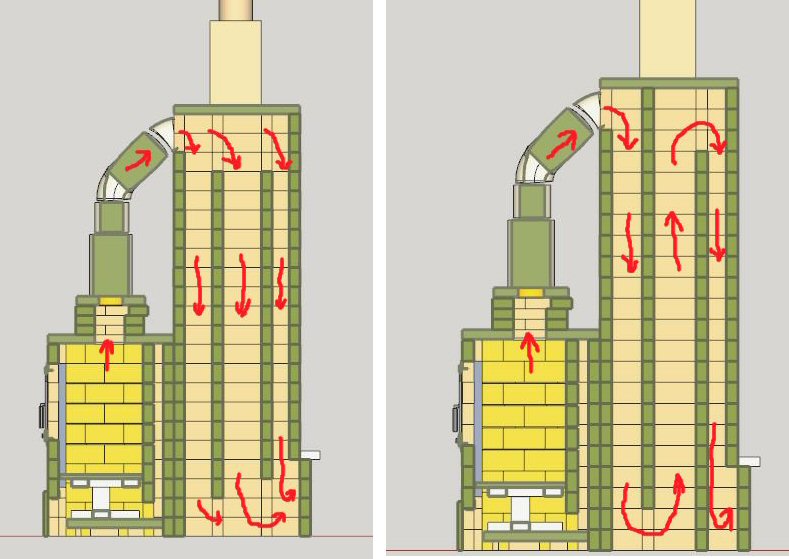 Here is an example from the MHA lab, showing the test heater running in two different heat exchanger configurations to see how the pressures and temperatures compare in theory and in reality. This data will help to tune the calculator to give a more accurate simulation of the heater over a wider range of conditions.
Here is Damien's recent report to the MHA and AFPMA tech commmittees:
Hi Norbert,
I'm happy to read that the Wood
Stove Design Challenge was a success and that the Condar
automation works fine.
We worked a lot on the Labmobil software, with Guillaume, please find the last
version attached:
All sensors are working fine now, but that was not
easy!
The signal was really bad, far from square:
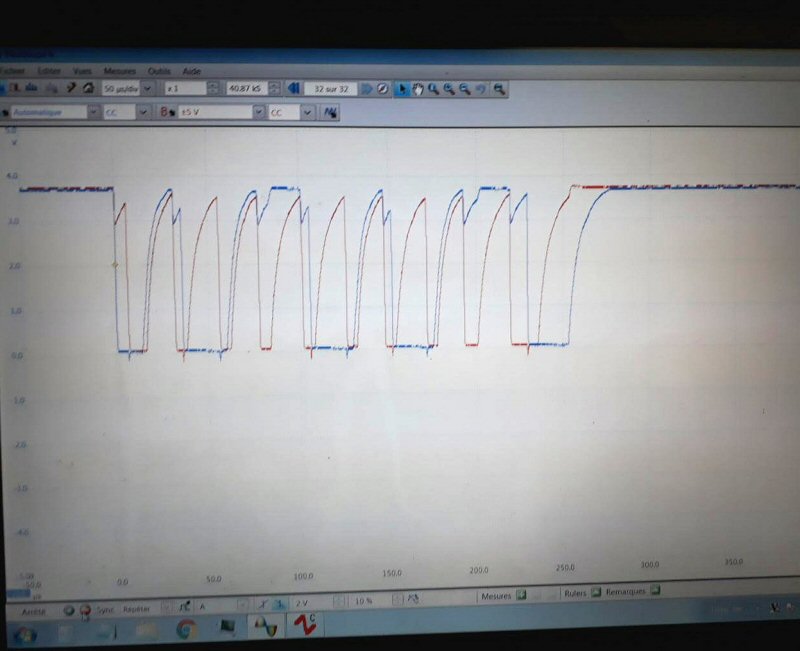
The I2C communication protocol doesn't like long wires coupled with multiple sensors on the
same bus, so we had to add a bus extender called P82B715PN. Now the signal waveform is nearly square :-)
We had a lot of issues with DaqFactory, but finally managed to get it all solved. DF has a lot of problem areas and debugging is really
long and difficult. We added I2C error management to avoid a value shifting, that
was the biggest part of the work.
We added with Christophe buffers on the pressure sensor to
stabilize the reading and reach a +/-1Pa instead of +/-4Pa. It's
the little boxes under the bricks, 0.5 liter with a very flexible
membrane (child's balloon).
Results were correlated with mechanical pressure sensor and are
OK. 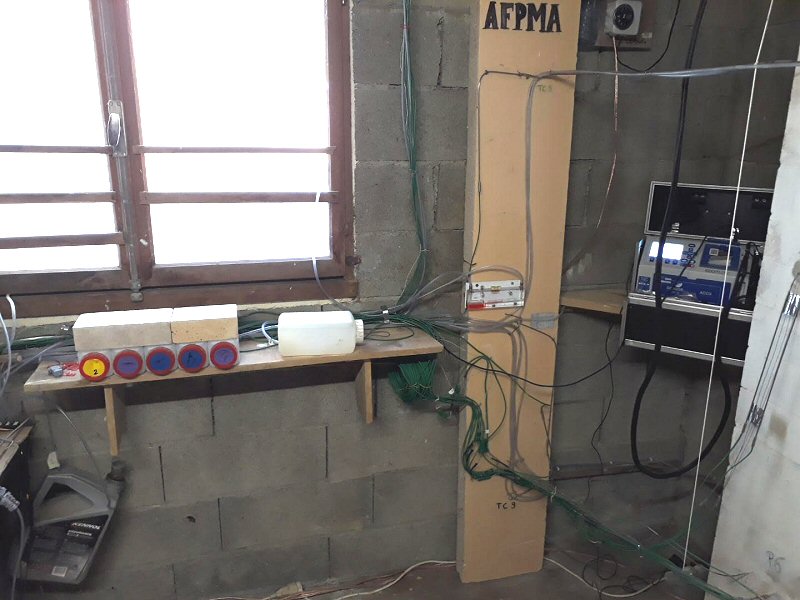
We added 10 thermocouples into the channels to establish a temperature
profile across the smoke section: 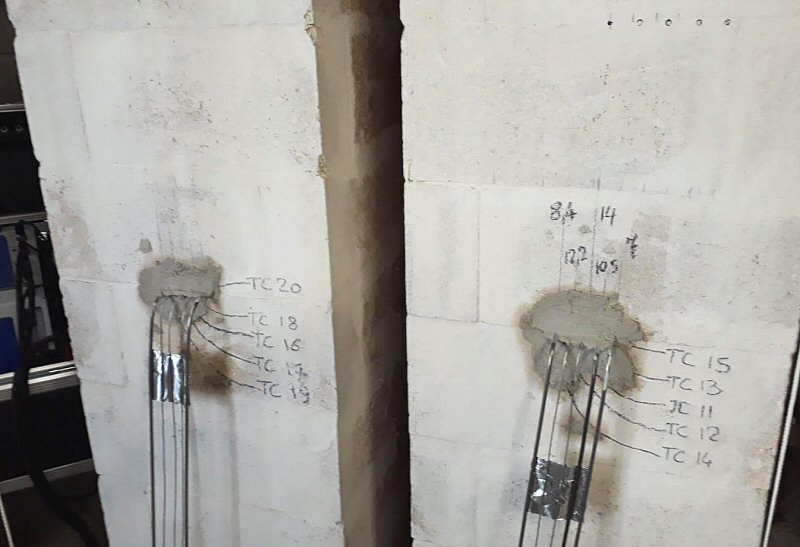
Finally, after something like 200 hours of work, we were able to
have a first workable analysis! : 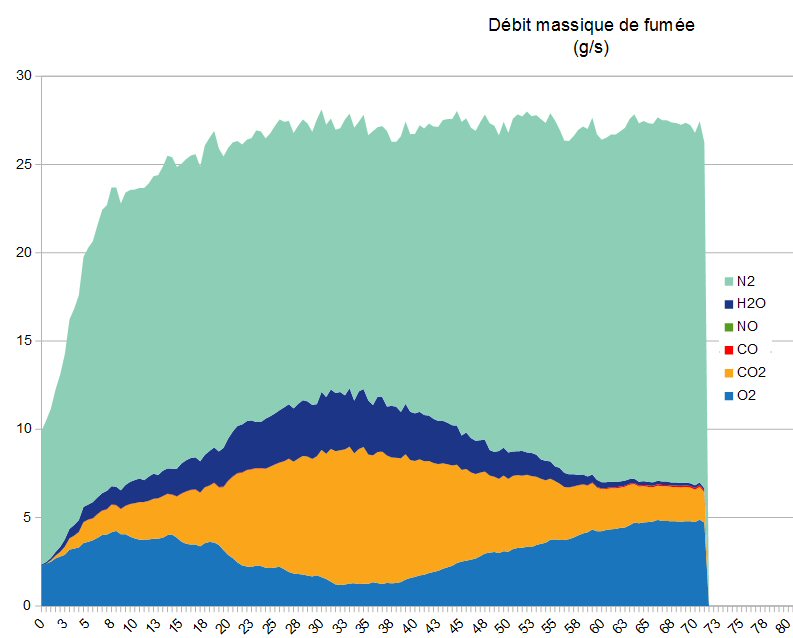
So I start comparing results with calculation predictions, and a
lot of problems appears once again :-D See the two attached spreadsheets. CalculPdM - v0.3.49 - Poęle test bas haut carré.ods 2018-11- 20 -Test.v.0.19.ods
I solved some of it, but there is still a lot to do.
I'm still questioning about how I could separate H2O produced by
combustion from H2O evaporate from wood moisture. This could help
me to solve the air speed difference at air entrance between
calculation and measure.
We had a very, very, very low O2 record:
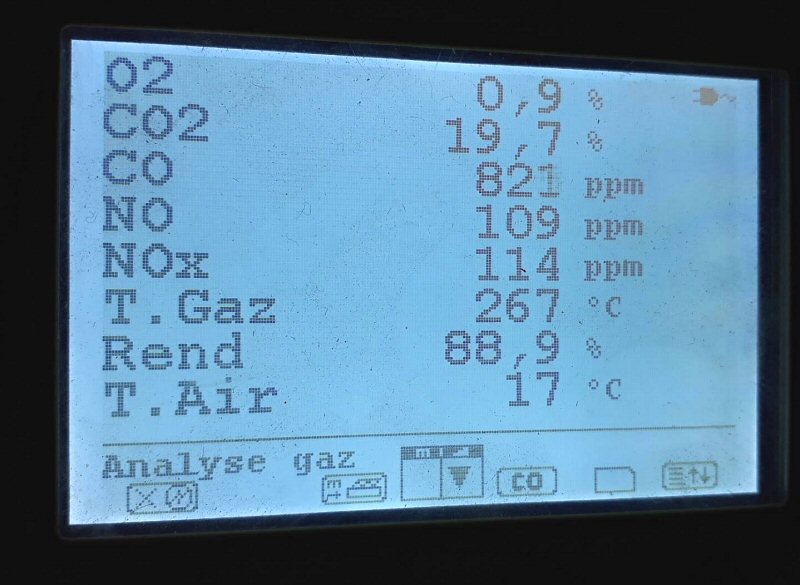
--
EI Damien Lehmann
La petite Trappe
17130 Montendre
05 46 48 62 37
06 64 89 68 25
www.poele-cuisiniere.fr
Siret: 524174307 00024
TVA intracom: FR 61 524174307
Membre actif de l'AFPMA
|