2018 Next Generation Woodstove Design Challenge
on The National Mall, Washington, D.C.
November 9 - 13, 2018
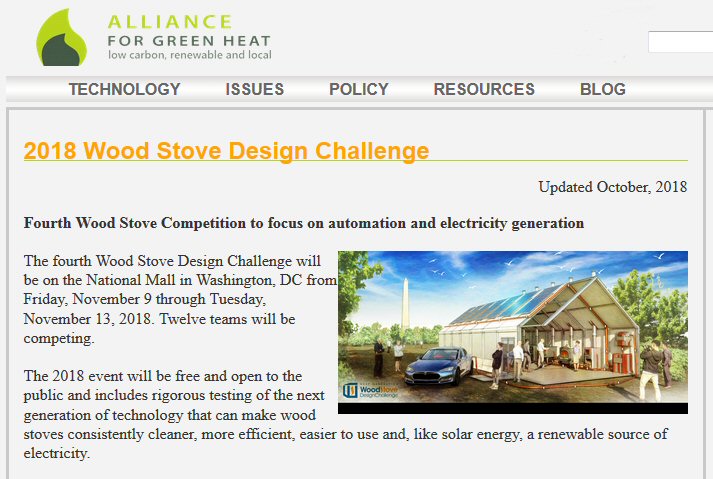
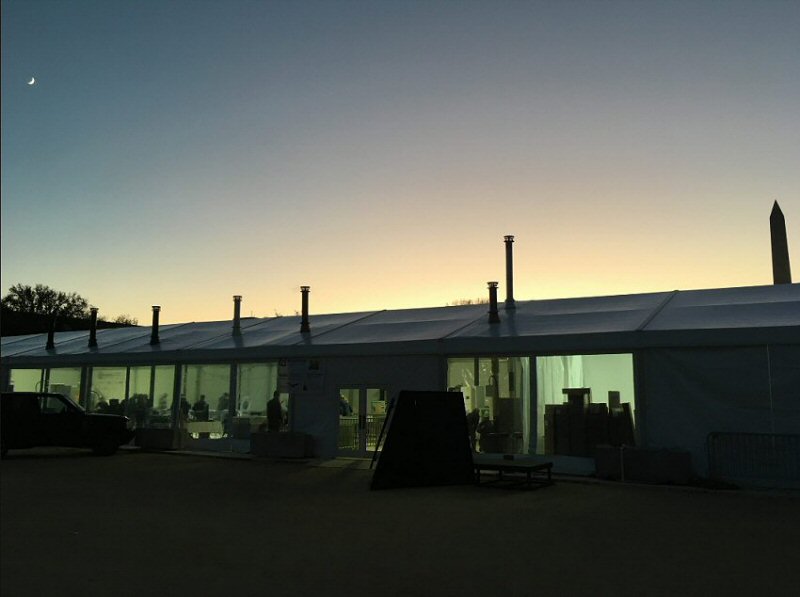
Photo credit: Jim Schalles
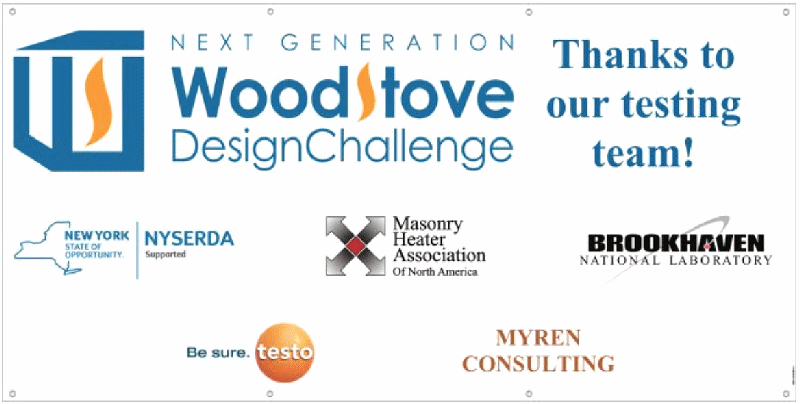
The MHA Tech Committee organized a 5 person testing team to send to the
event.
We
brought 3 complete Condar PM sampling systems, and conducted a total of
15 three hour test runs over the course of 5 days. We were
tasked with combustion testing of the thermoelectric stoves. Brookhaven
National Laboratory had responsibility for testing the
automated stoves, with funding help from NYSERDA.
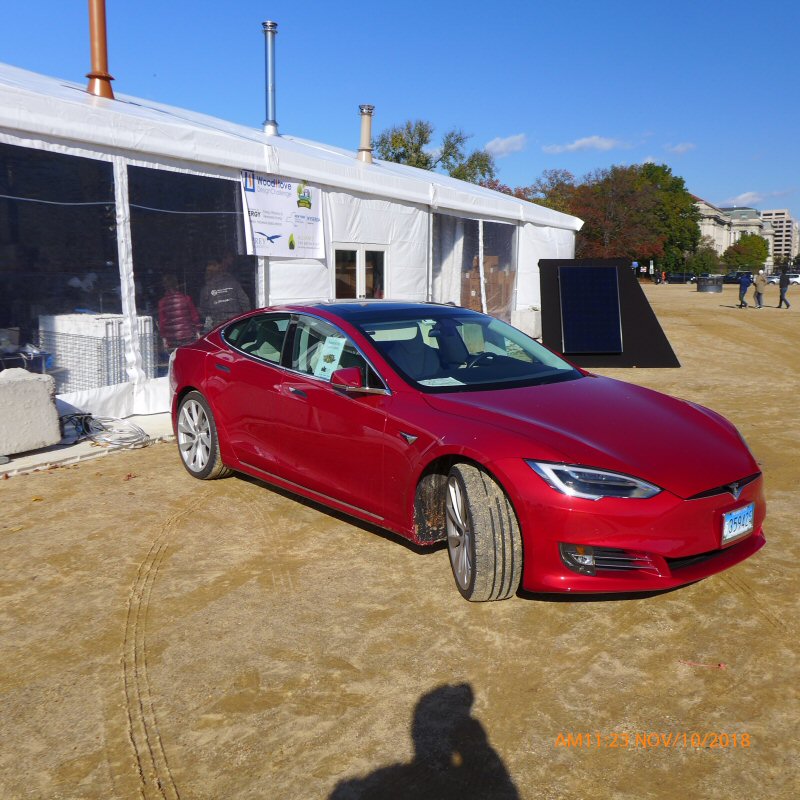
Tesla S being charged by a MES
pellet boiler with a 5kW electric output.
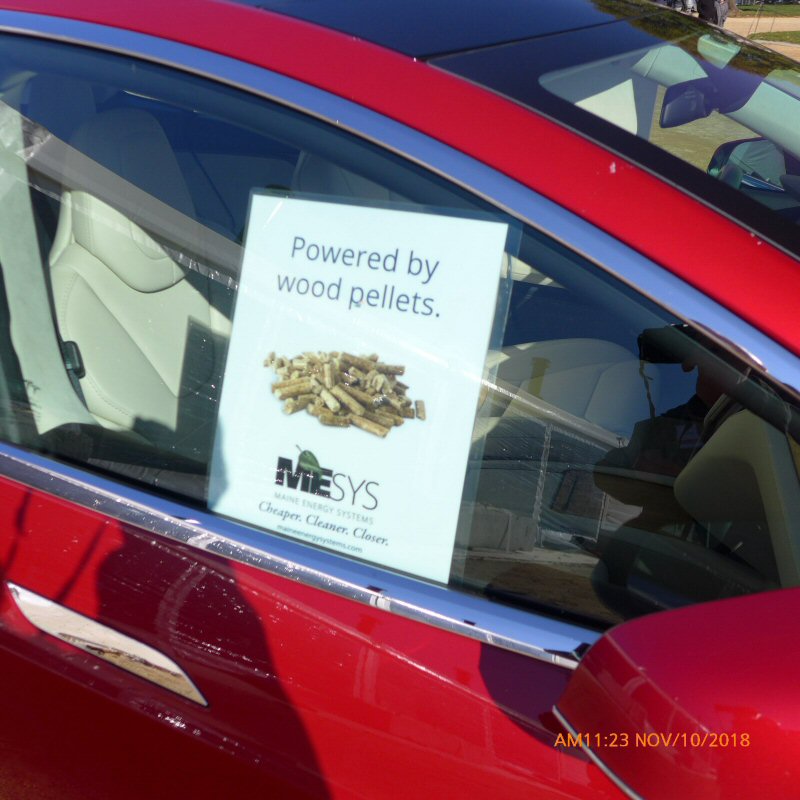
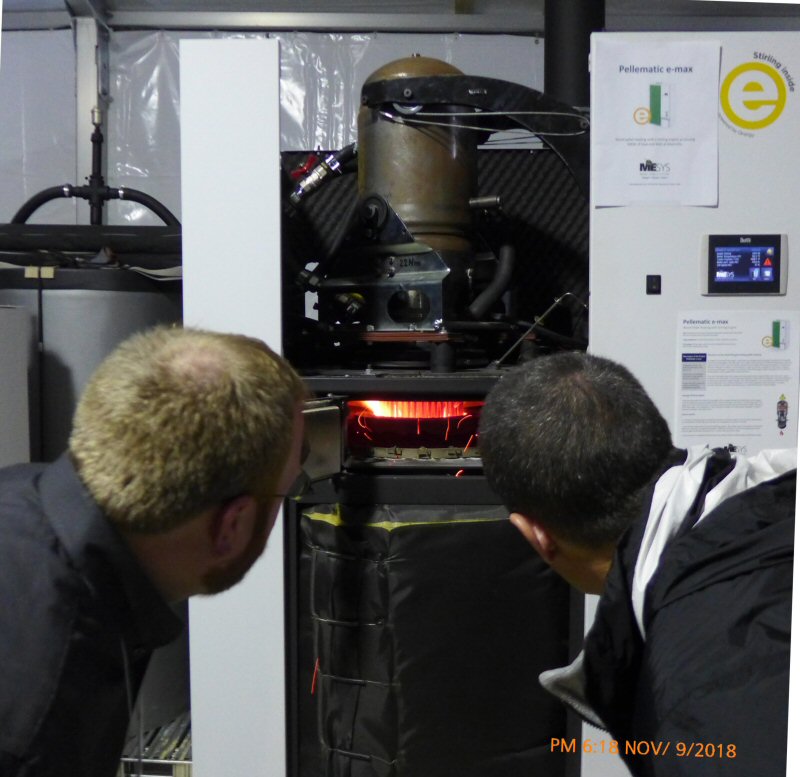
Maine
Energy Systems
AutoPellet boiler with optional Stirling engine generator add-on was a
highlight. They were there by special invitation as a demo, since
boilers were not elible for the competition..
They have a unique
achievement in having brought CHP (combined heat and power) down to a
near-domestic scale on a semi-commercial level. The unit is expensive
at the moment, but they are commercially available in Europe and have
logged many hours on them at client sites. This is the first time I
have seen this combination of user friendly, real world proofed, and
domestic scale electric power output from pellets.

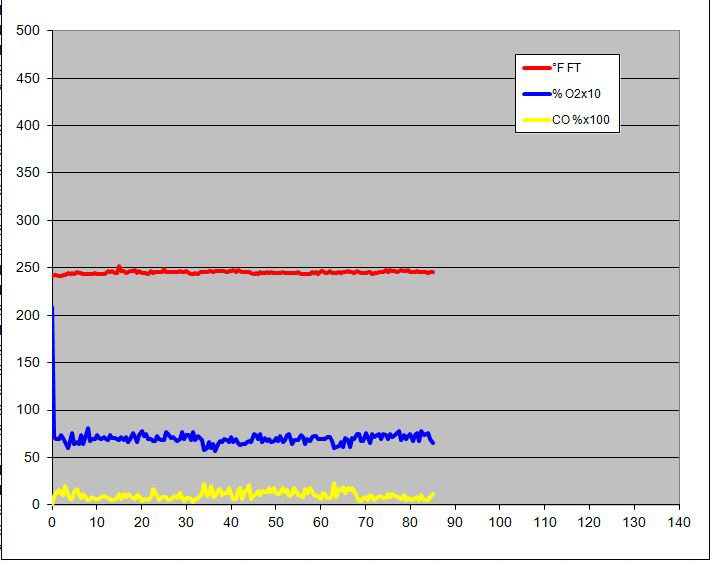
Stack gas analysis graph.
Low stack temperature (250 F), very low oxygen (O2, blue line) and low carbon monoxide (CO)
means high efficiency.
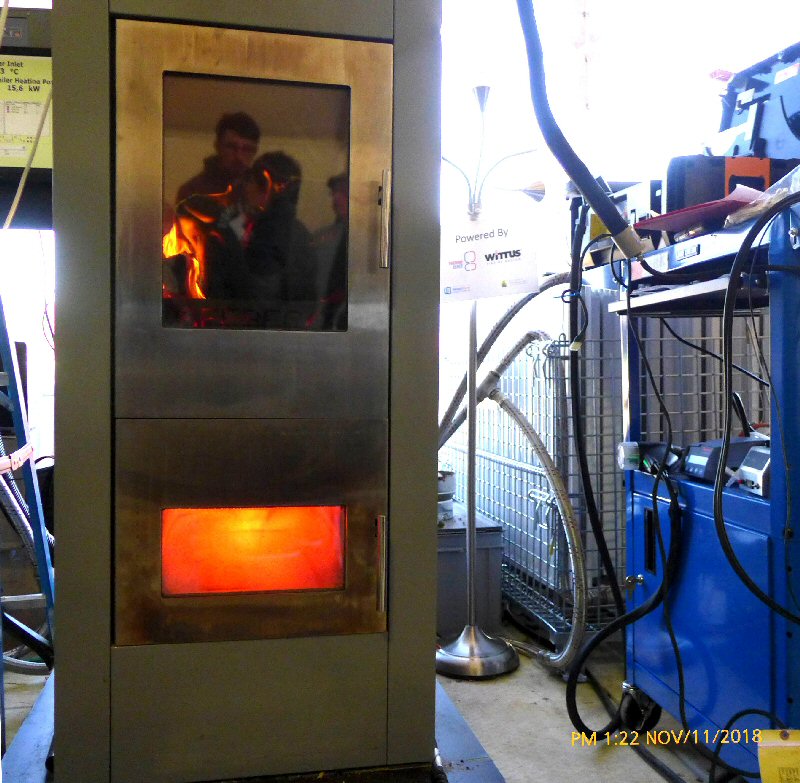
Wittus
automated downdrafting cordwood prototype stove is optimized for
electricity production by using water cooling of the TEG
(thermoelectric) cells. It also has a catalyst in the lower chamber.
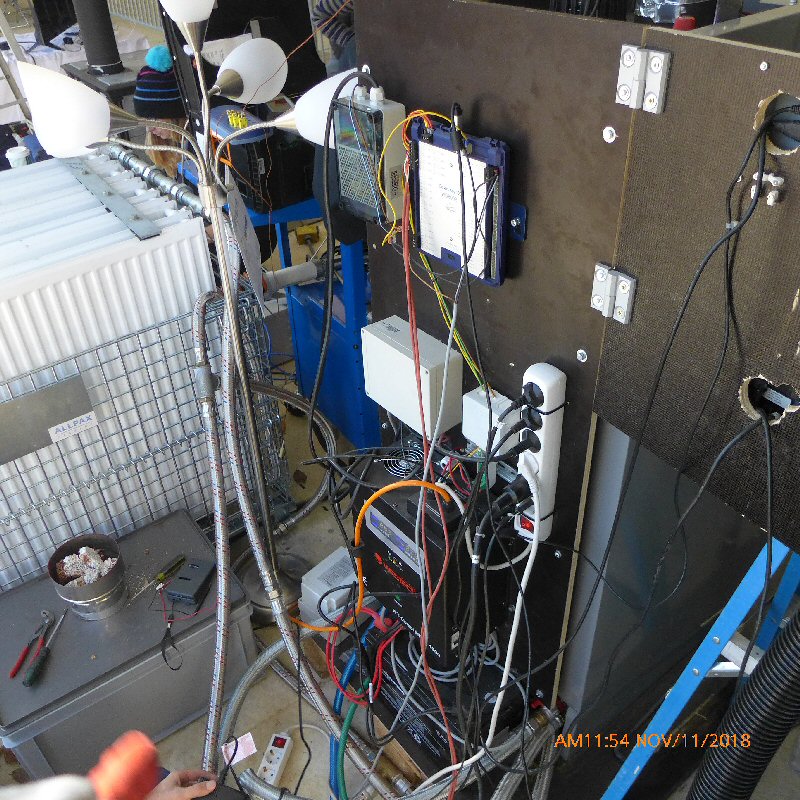
View from the rear. On each side is a large bank of water radiators.
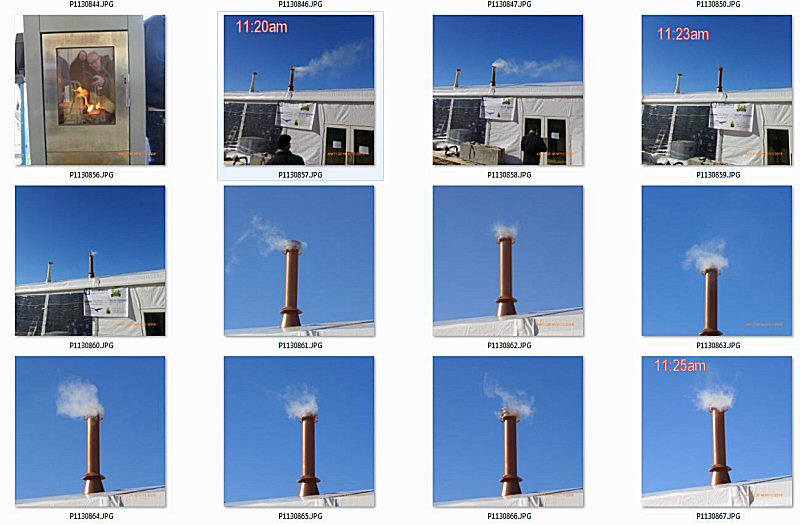
Startup
sequence. Smoke is visible at 11:20 am at startup. By 11:23, no smoke
is visible. Shortly afterwards only steam is coming out of
the
stack, as evidenced by the lack of the plume that is visible on startup.
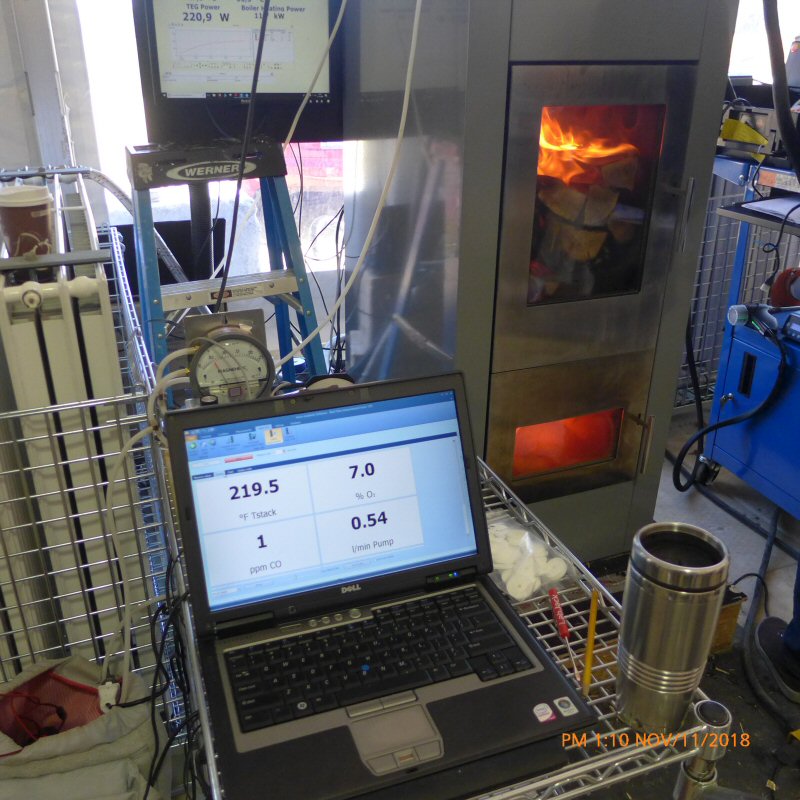
Segments of the burn had the lowest CO I have ever seen (it actually
got to 0 for a few seconds).
Low stack temperature, low excess air (O2), super high efficiency.
Producing 218 watts of TEG (thermoelectric) power (rear screen).
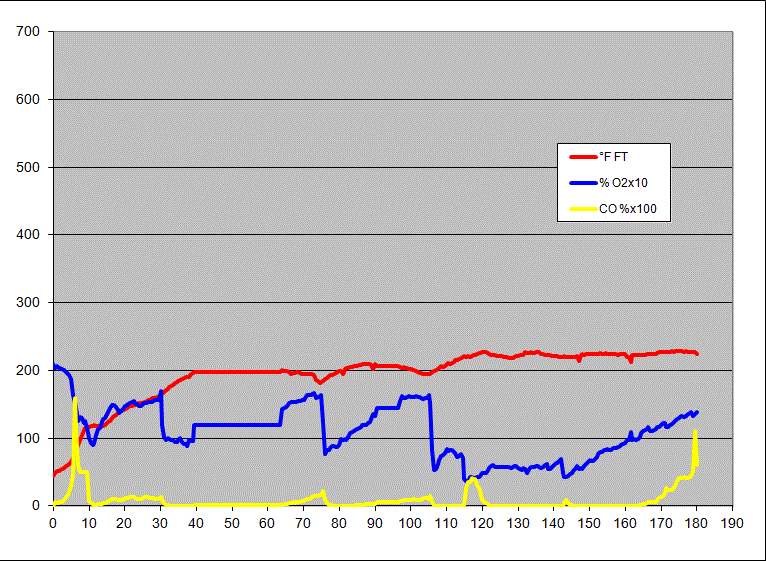
Stack gas graph. We lost data from minutes 40 to 65. We interpolated
the lost data, as shown by the flat lines.
The 3 reloads are clearly visible as big dips in the blue oxygen line.
This was a trial of a shortened version of the new Integrated
Duty Cycle (IDC) testing protocol under development by
NESCAUM to better simulate real world use in cordwood testing.
Therefore,
the particulate numbers are not directly comparable with EPA laboratory
certification numbers, which one might expect to be lower.
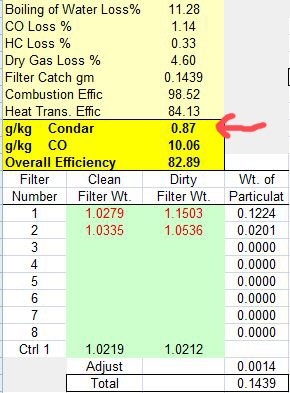
PM and CO are were the same range as we have measured on masonry
heaters with the Austrian
eco-labelled firebox.
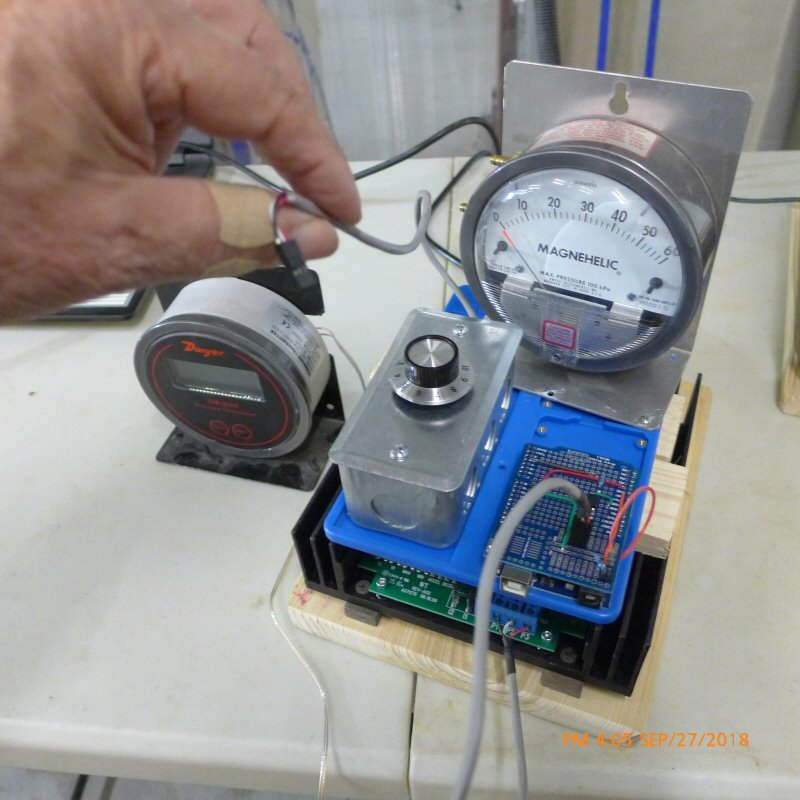
We
spent several months developing and testing this automated controller
for our Condar
portable dilution tunnel PM emissions sampler. It
lessened the work load on our crews to a much easier oversight function
for the equipment, rather than manually having to adjust the
flow
control for the sampler over each 3 hour test period.
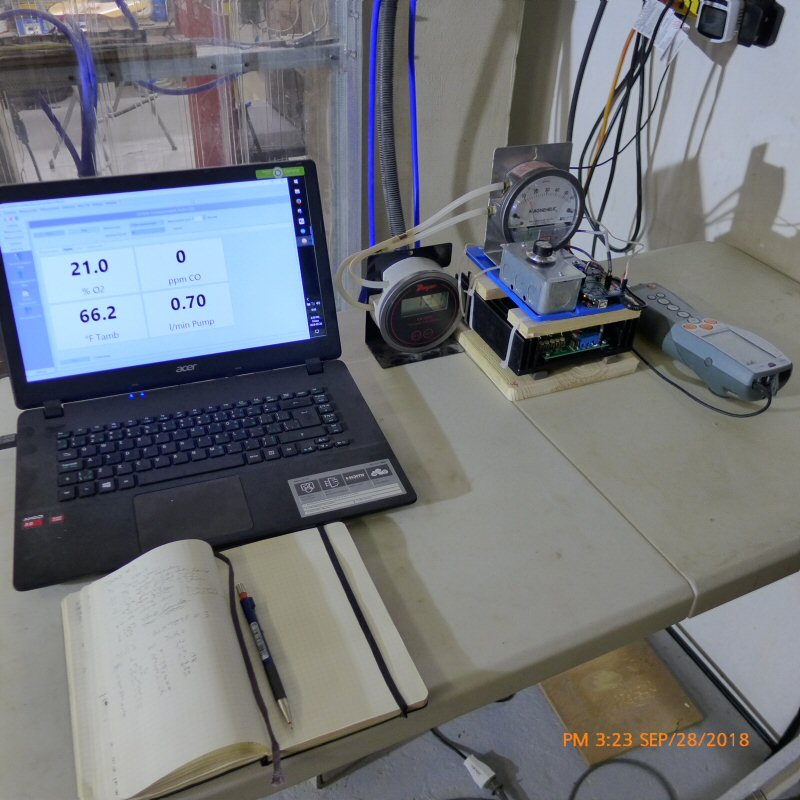
Testing the 3 new controllers at the MHA Lab
in Shawville, Quebec, prior to the event.
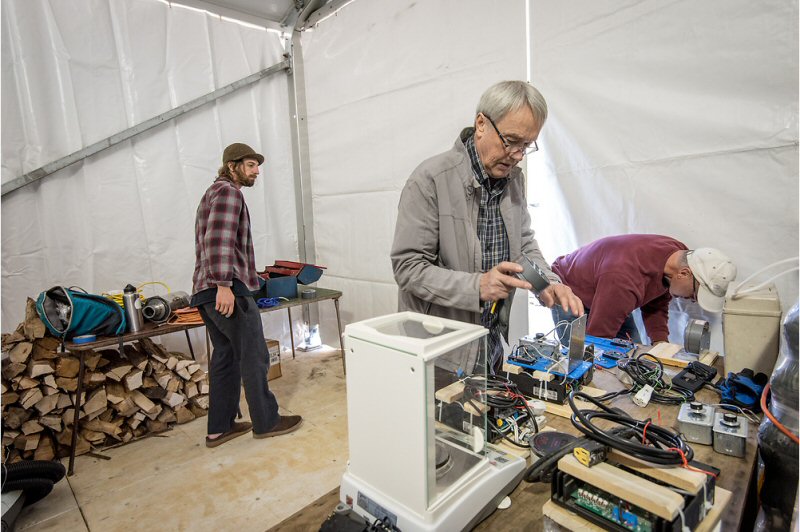
Arriving
at the tent on The National Mall. Equipment travelled
from sites
in Quebec, Massachusetts, Minnesota, and Maryland. "Some assembly
required" Photo credit: Kittner for Brookhaven National Lab
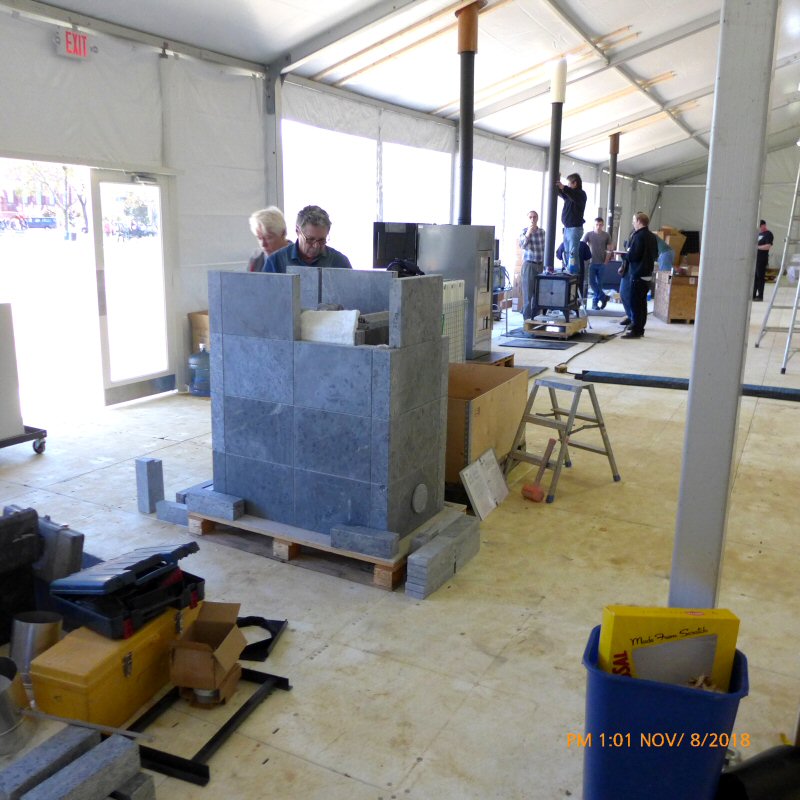
Assembling a Tulikivi
demonstration heater, that was used to keep the overnight security
crews warm during some chilly weather. It travelled from the Tulikivi
US distribution distribution warehouse in Charlottesville, VA.

Testing team from Brookhaven National Laboratory setting up their
equipment.
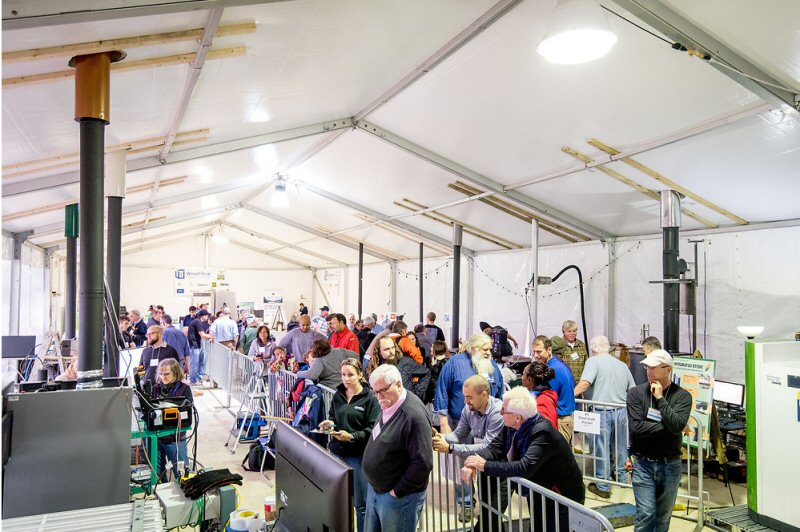 Open to the public and testing in full swing. Check out this great article about the public's impressions at the event. Photo credit: Kittner for Brookhaven National Lab
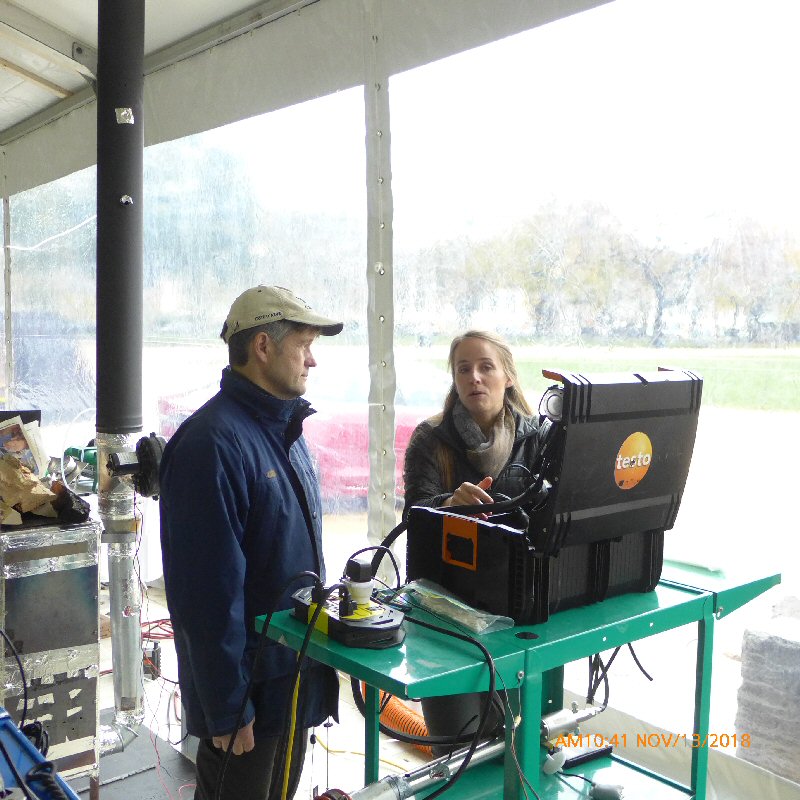 Boris Kukolj, head of Tulikivi North America Rebecca Trojanowski, test engineer at Brookhaven National Laboratory
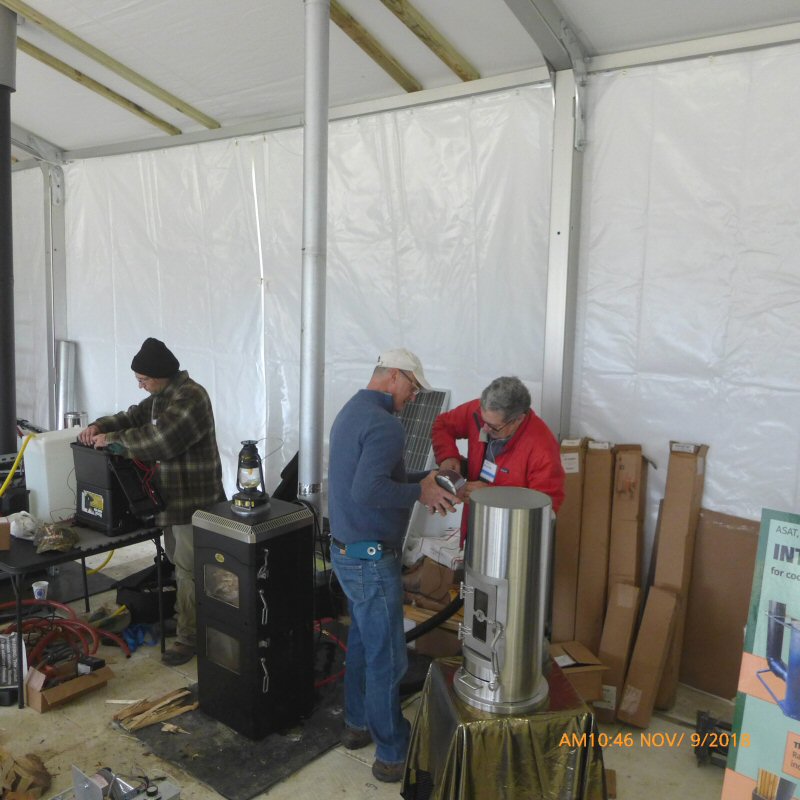
Mark Seymour
and Ron Pihl
setting up our equipment on the Kd3
downdrafting thermoelectric stove.
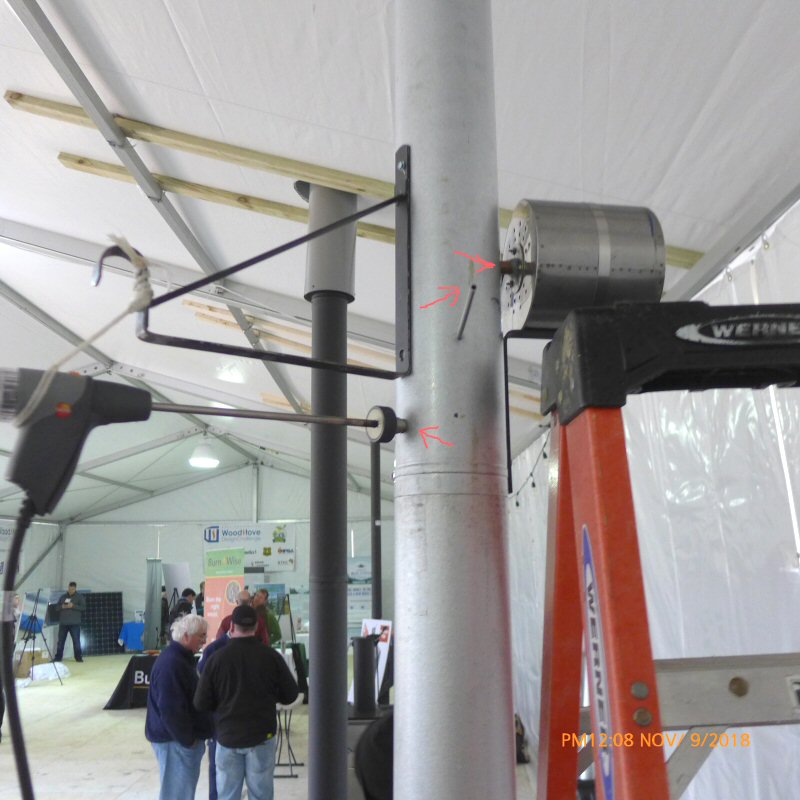
Location of the 3 holes drilled into the stack for:
- Condar
portable PM sampler
- stack pressure reference port
- Testo
330-2 flue gas sampling probe
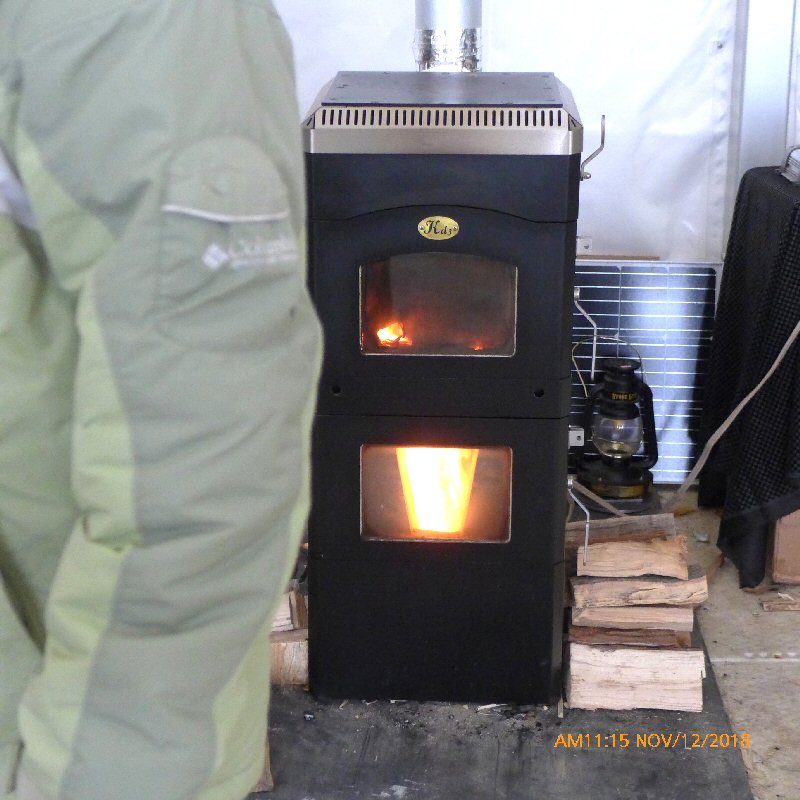
It
has a very innovative hot side heat exchanger scheme for the TEG's.
After the downdrafting flame finishes combustion and turns the corner,
a thick copper fin that is directly in the gas path is joined to an
aluminum plate that is out of the gas path.
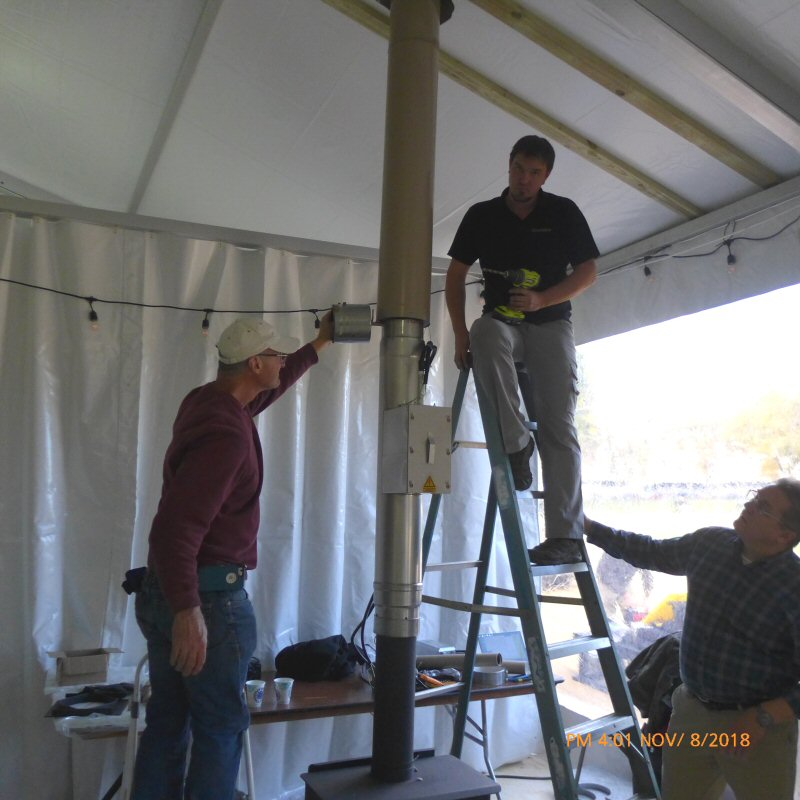
Setting up a demonstation test on the Swiss OekoSolve
electrostatic precipitator.
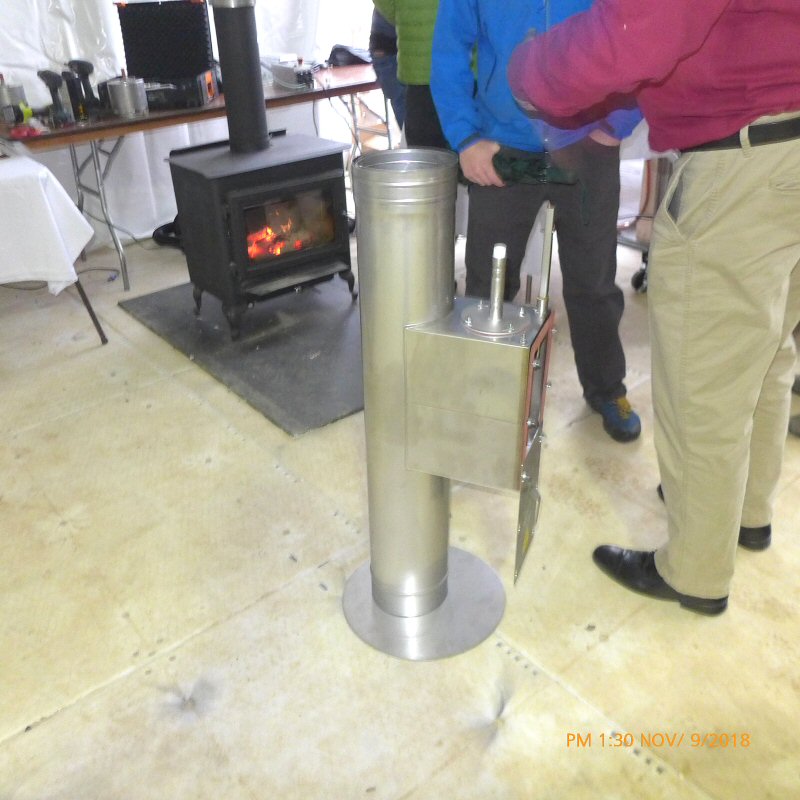
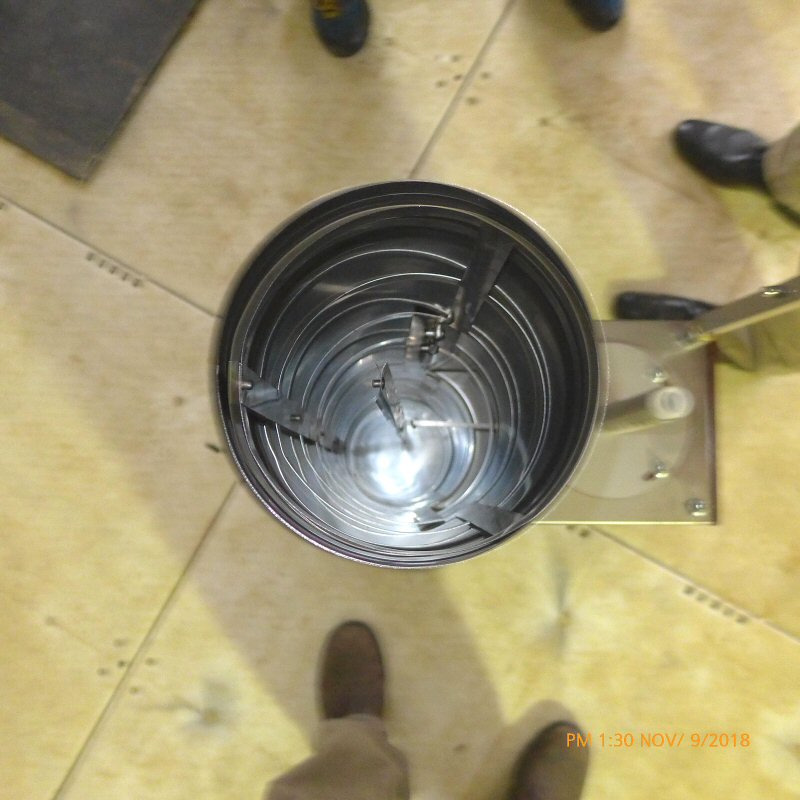
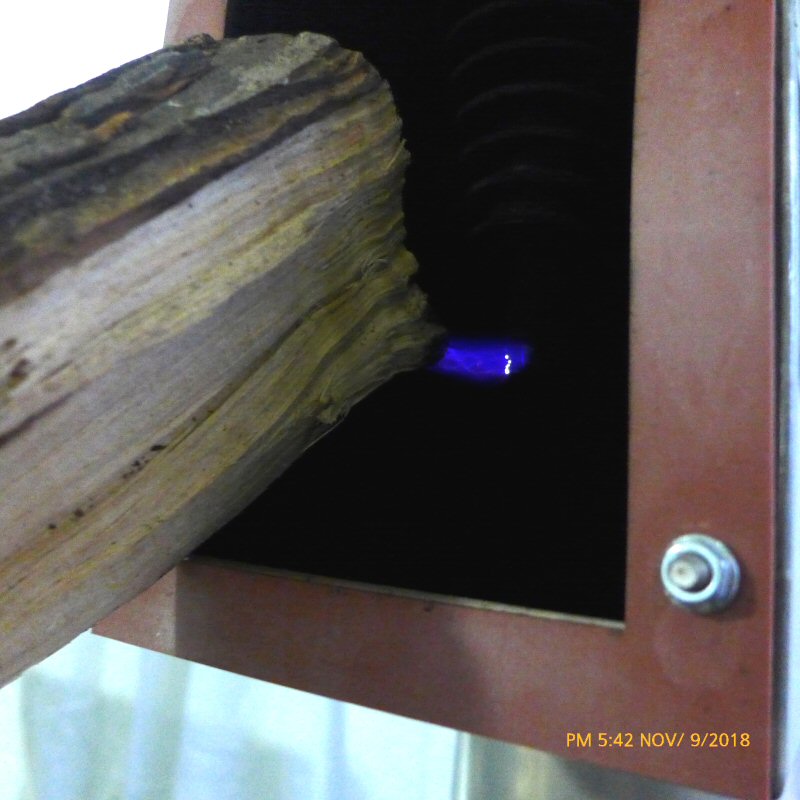
Demonstration of 30,000 Volt plasma cloud arcing over to a piece of
firewood.
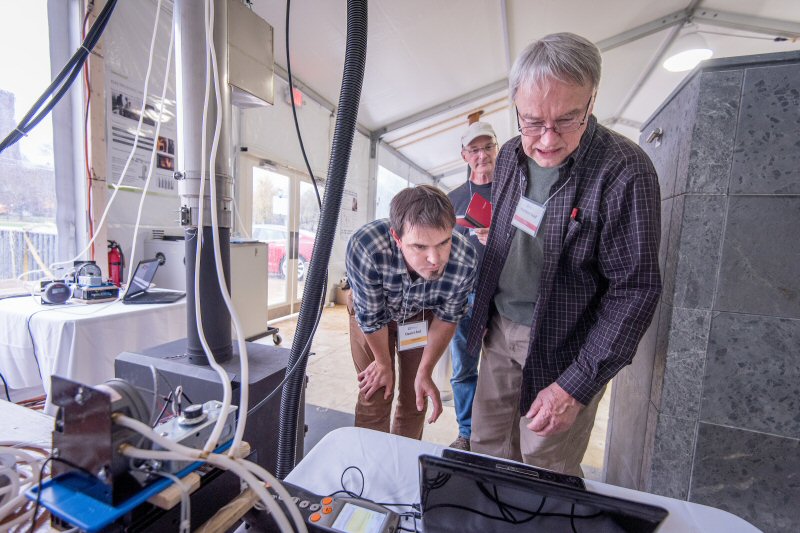 Daniel Jud from Oekosolve checks the Testo readings Photo credit: Kittner for Brookhaven National Lab
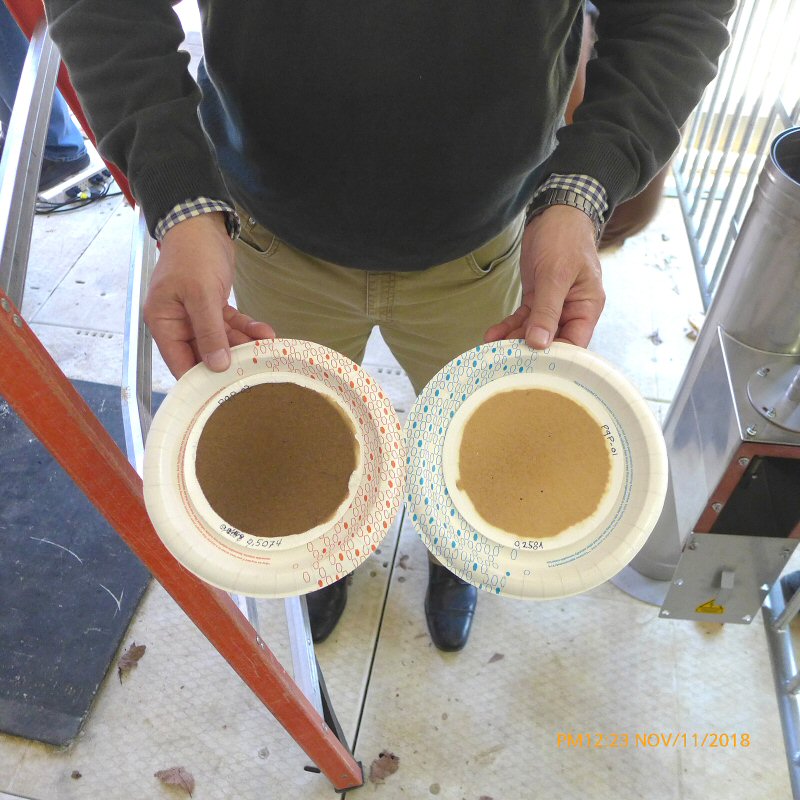
We
ran 2 Condar samplers, switching them on and off at 6 minute intervals,
in synch with the precipitator. The old technology stove
was quite
dirty, as shown by the yellow strong smelling organics on both filters.
The PM reduction on the precipitator "on" filter on the right
was 62%. Test Report
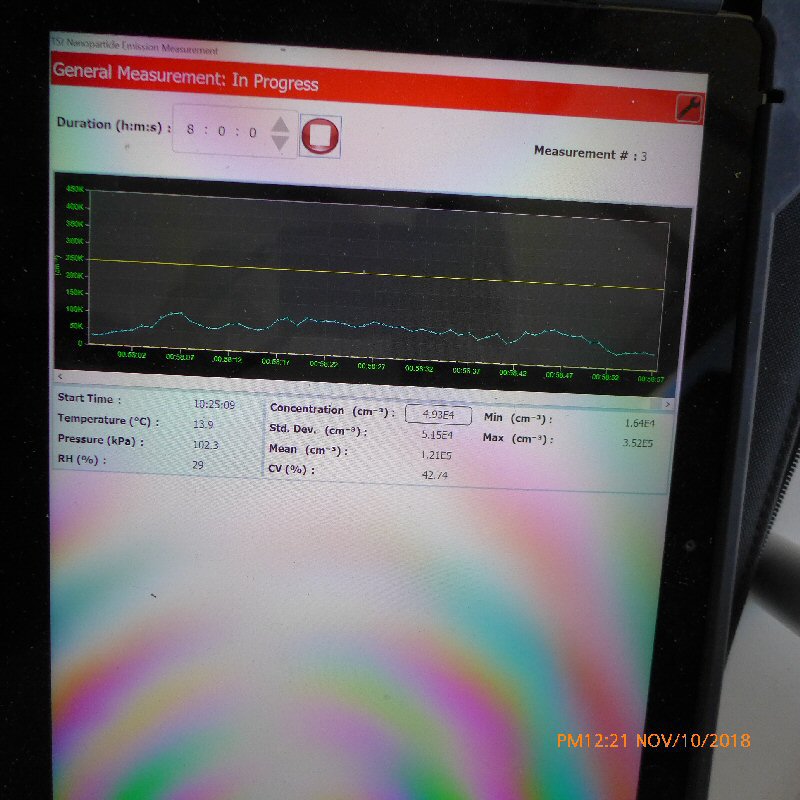
NY
State Dept. of Health brought along a real-time nano particle counter.
It has a cutoff at 1 micron (1/1000 of a millimeter), and counts down
to the nanometer range. It showed a reduction in the 80% range of nano
particles when the precipitator was turned on.
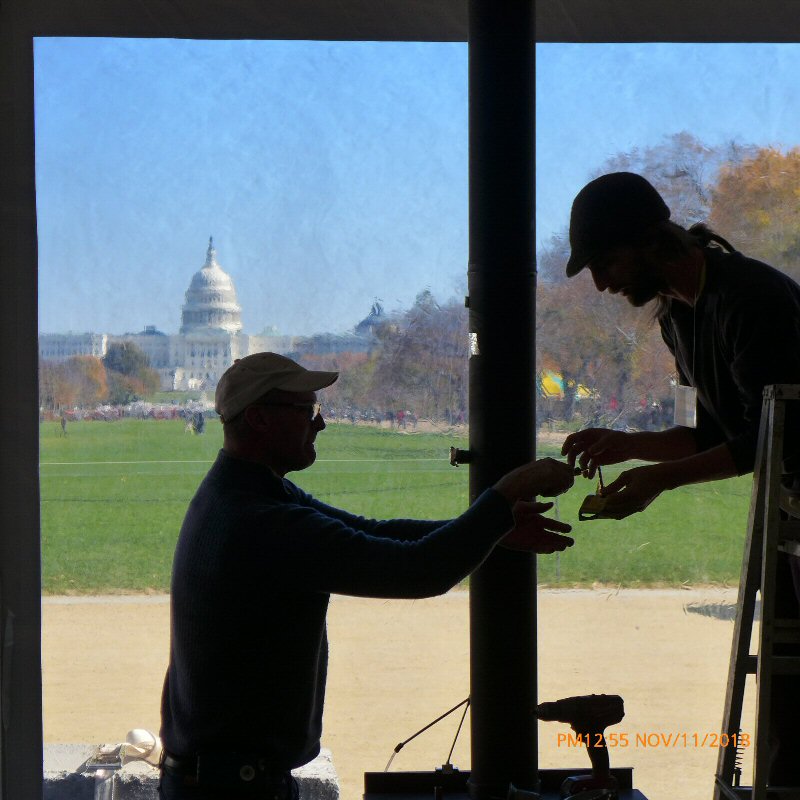
Mark Seymour and Jim
Schalles prep the chimney on a stove with the VcV
(Venturi-Controlled Valve) from New Zealand. It provides automated
primary and secondary air control, without electronics or power
requirements.
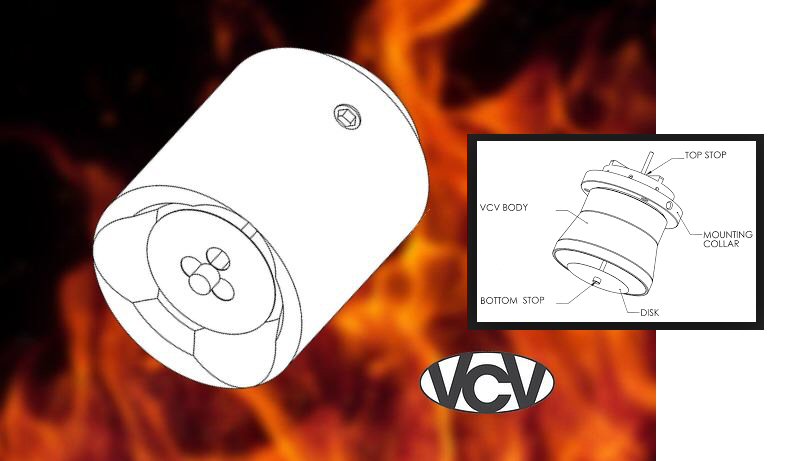
A
thin metal disc slides on a rod. Gravity holds the air supply open. As
the stove warms up and draft builds up, the disc is pulled up the rod
by air pressure, and finds a balance point. There is a separate valve
on the primary and secondary air supplies.
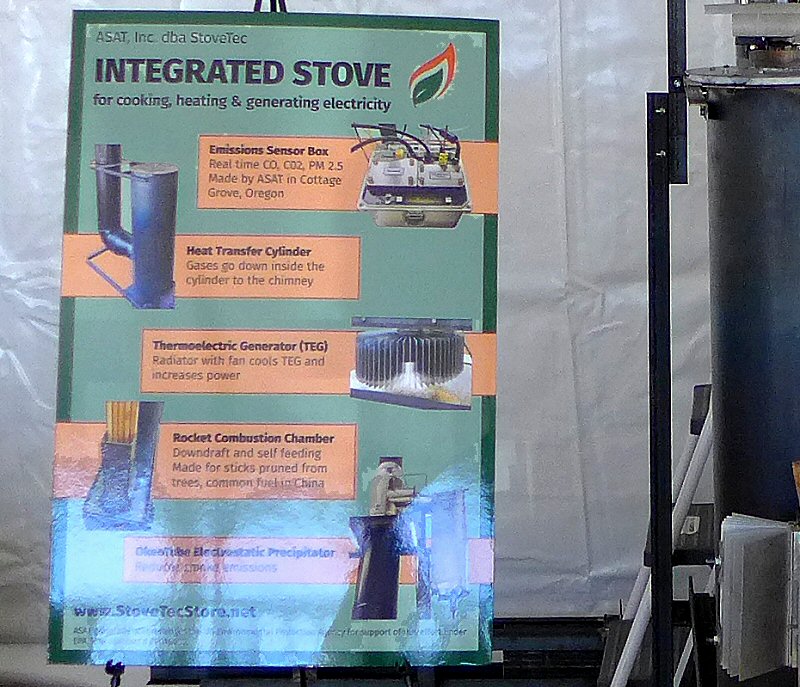
Aprovecho
Integrated Stove
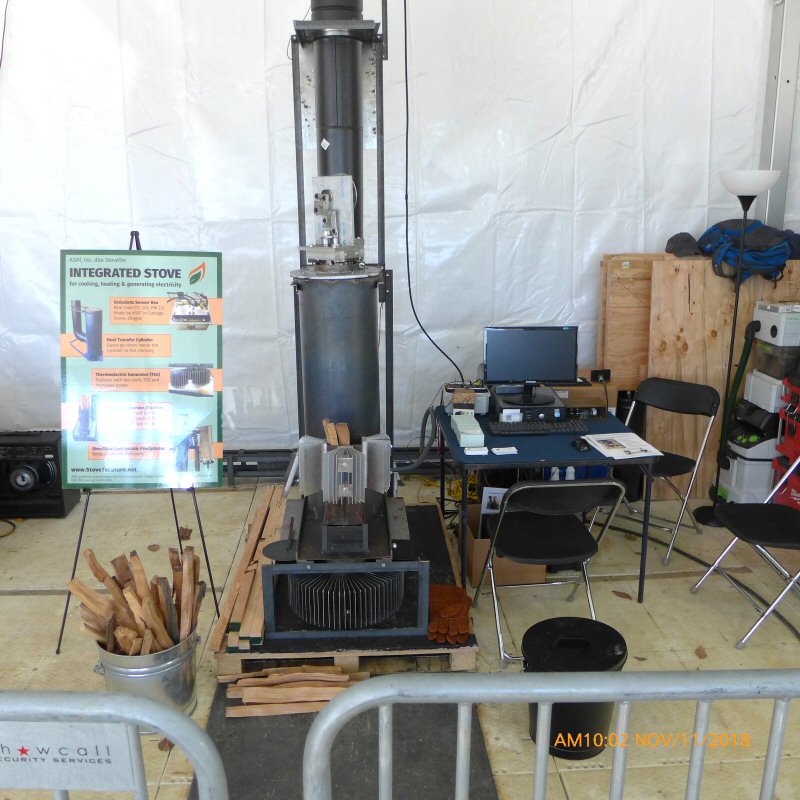
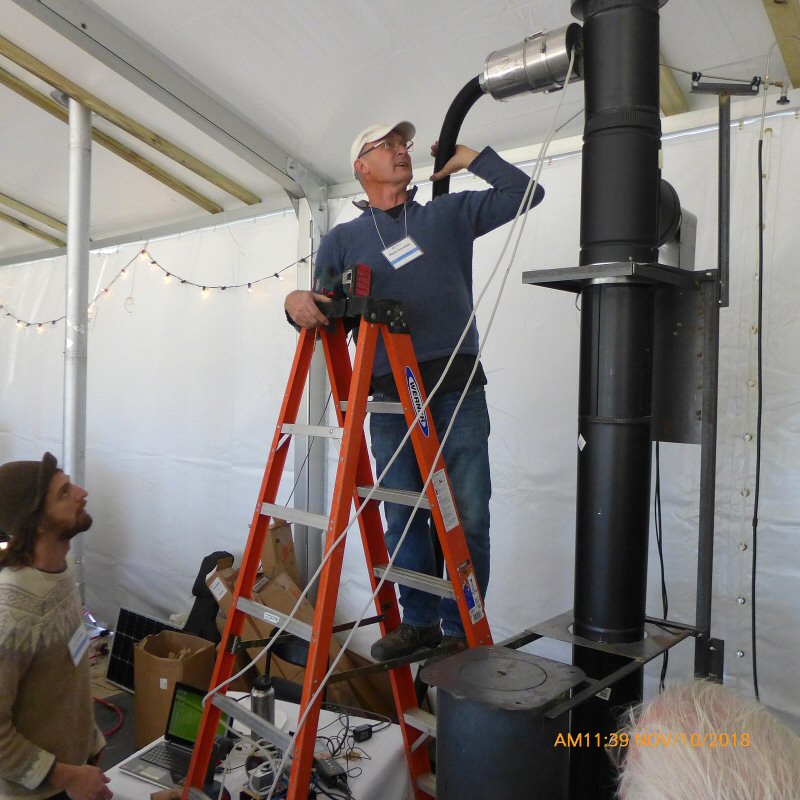
A
14' hose connects the Condar to a Kenmore vacuum sitting outside the
tent. The Kenmore is controlled by MHA's new automated Condar
controller.
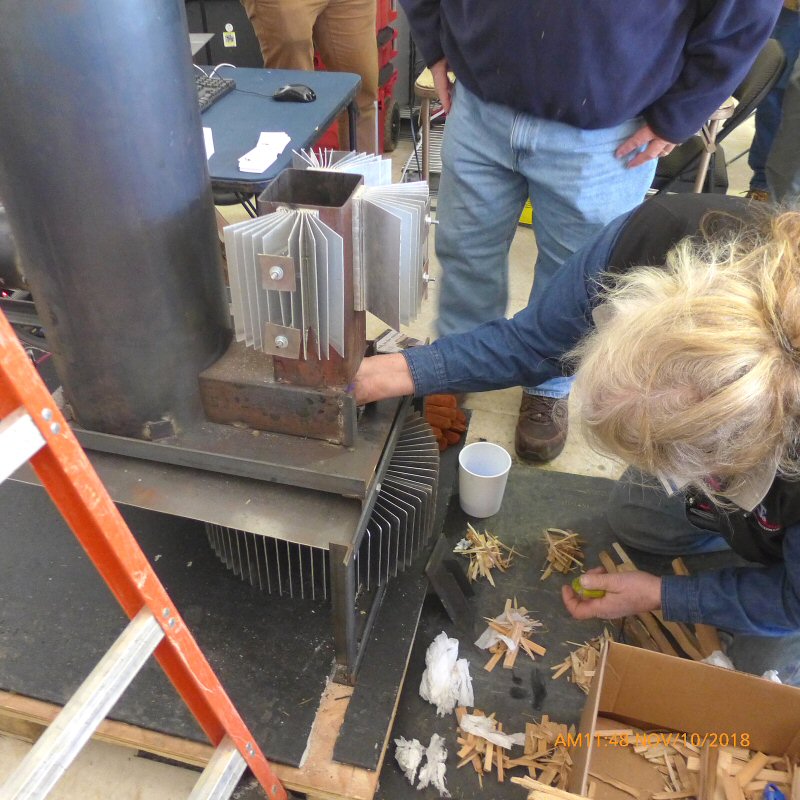
Ben
Myren did
the fueling on the TE (thermolelectric) stoves. Here he starts up the
prototype rocket stove from Aprovecho. It is designed for a specific
application in China, and has air cooled TEG modules with a large
cooling fin area. It also features an OekoSolve electrostatic
precipitator on the exhaust.
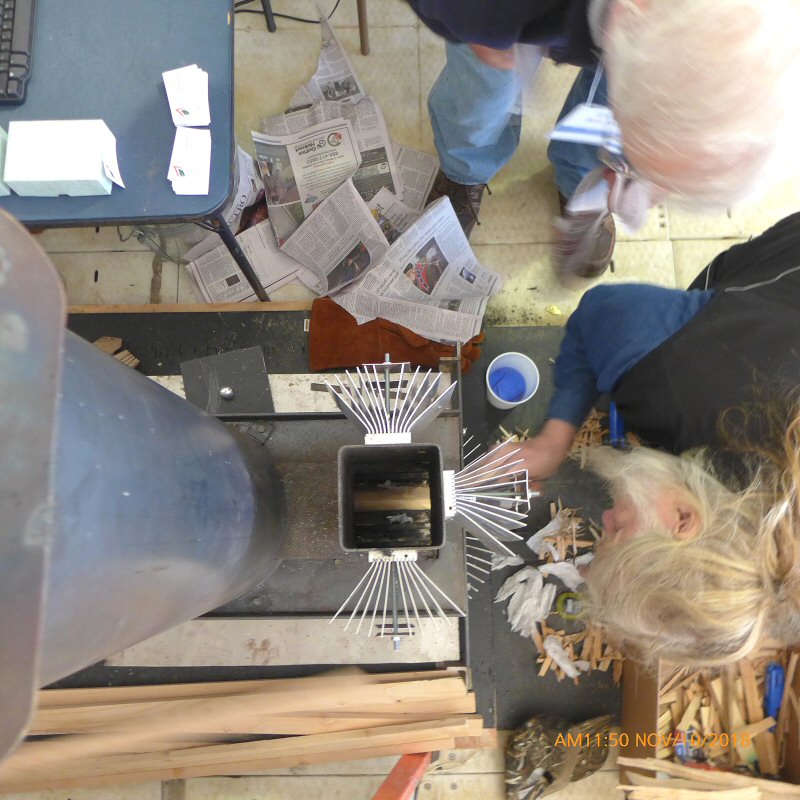
A bit of help was needed from the blue alcohol gel in the cup next to
Ben.
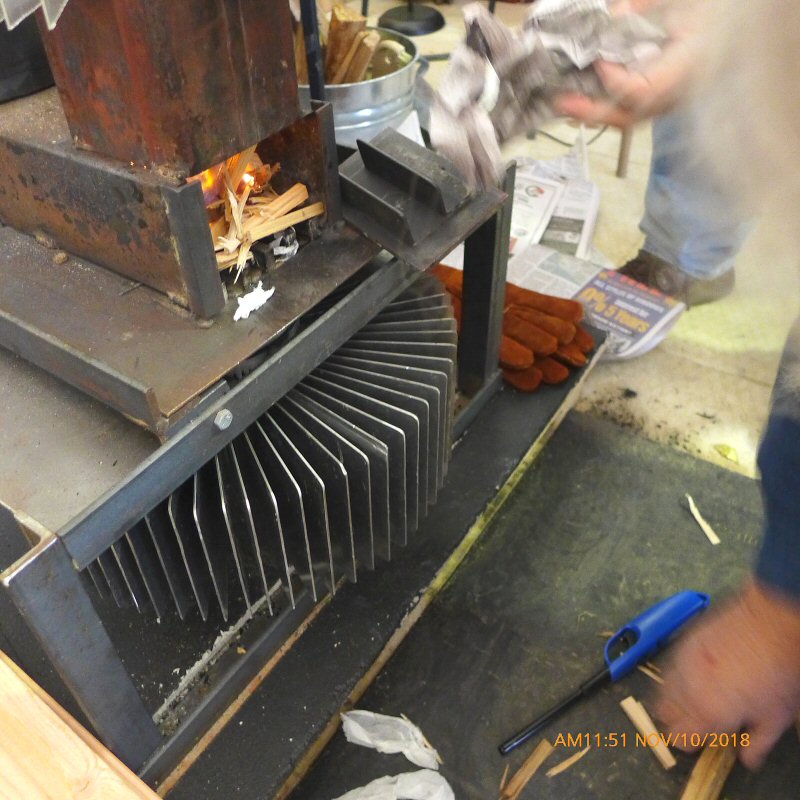
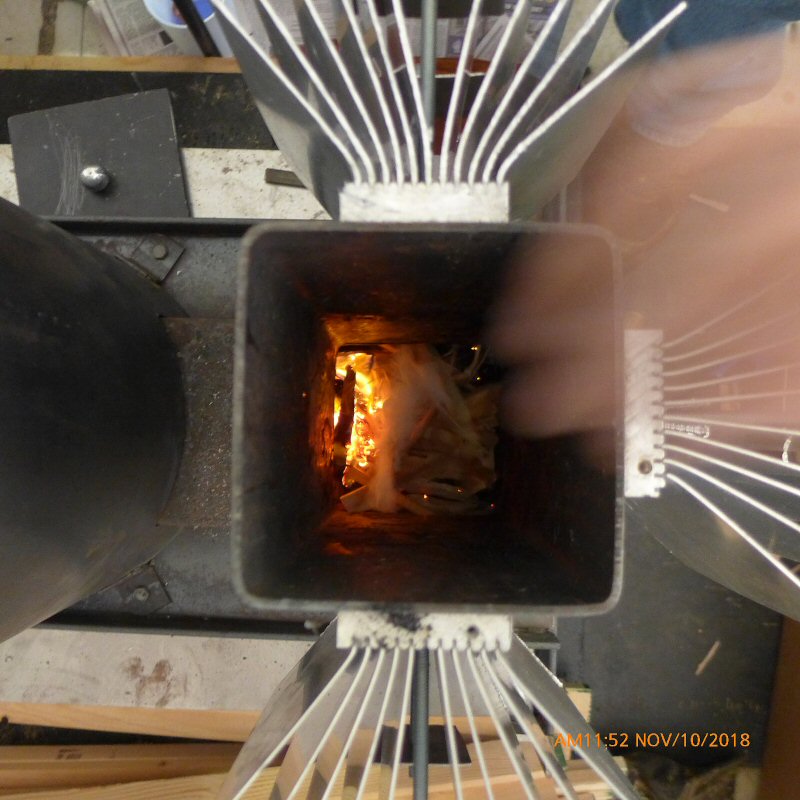
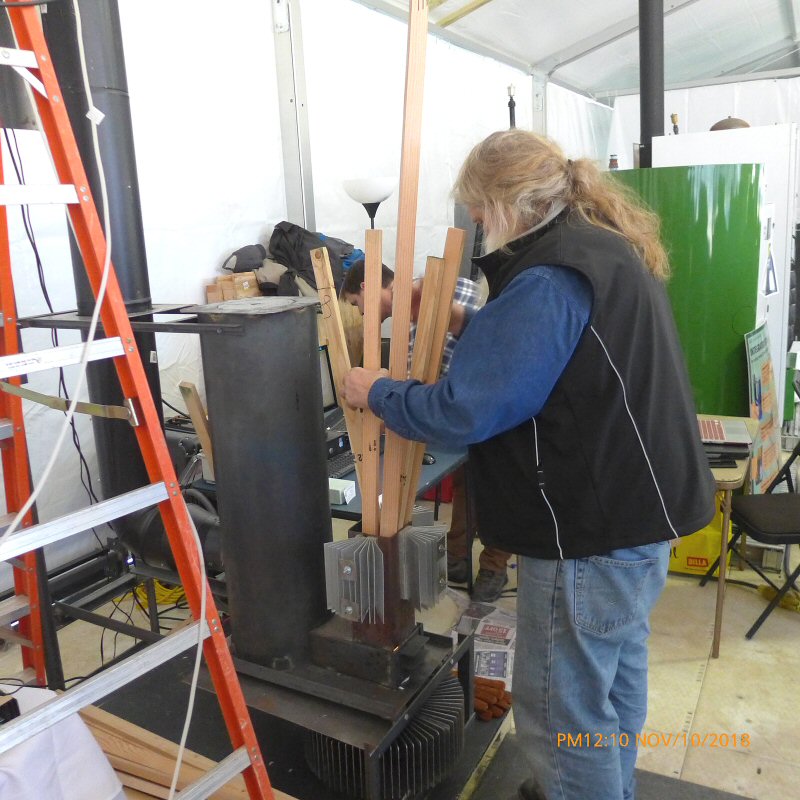
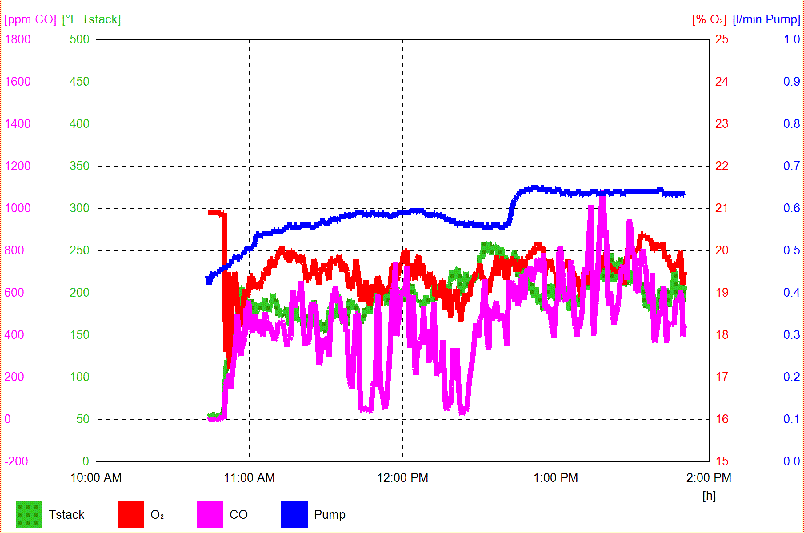
Stack gas analysis graph automatically generated by the Testo EasyHeat data logging software.
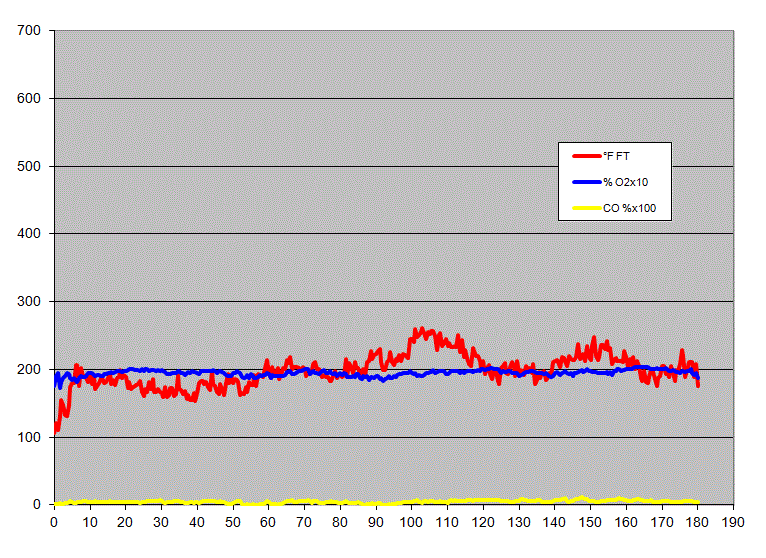
Normalized graph in MHA standard format, for comparison purposes with
other tests.
Note the blue O2 line is very close to 20%, indicating very high excess
air on this run.
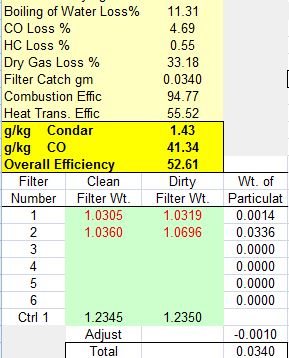
Condar spreadsheet summary. Compare with Run 2, below.
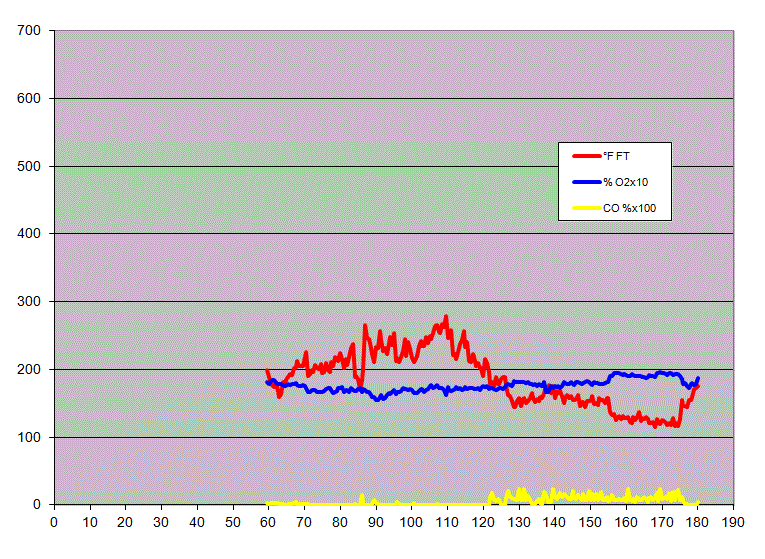 Normalized graph for run #2. The first hour of data was lost due
to a computer glitch.
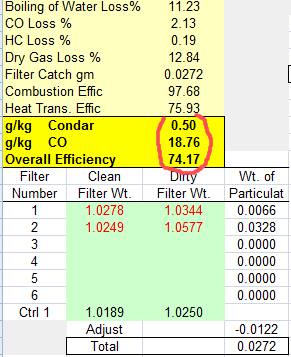
Condar summary.
The electrostatic precipitator was not functioning in Run 1.
Run 2 had the precipitator operating and has lower PM.
Run 1 had high excess air and high CO, so was a different type of
burn.
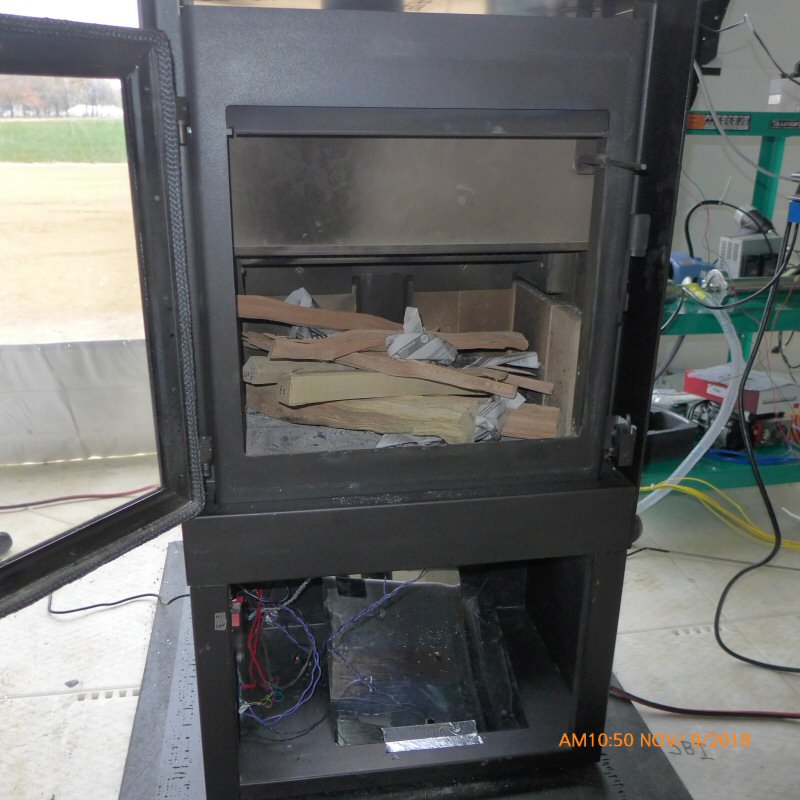
SBI entered
a prototype fireplace stove that was completely automated, based on 2
simple sensors - flue temperature and door open/closed. A sophisticated
logic board regulates 2 air control motors to keep the stack
temperature constant and boost the fire on a cold start. Their stove
also had the best fire viewing of all the stoves in the event.
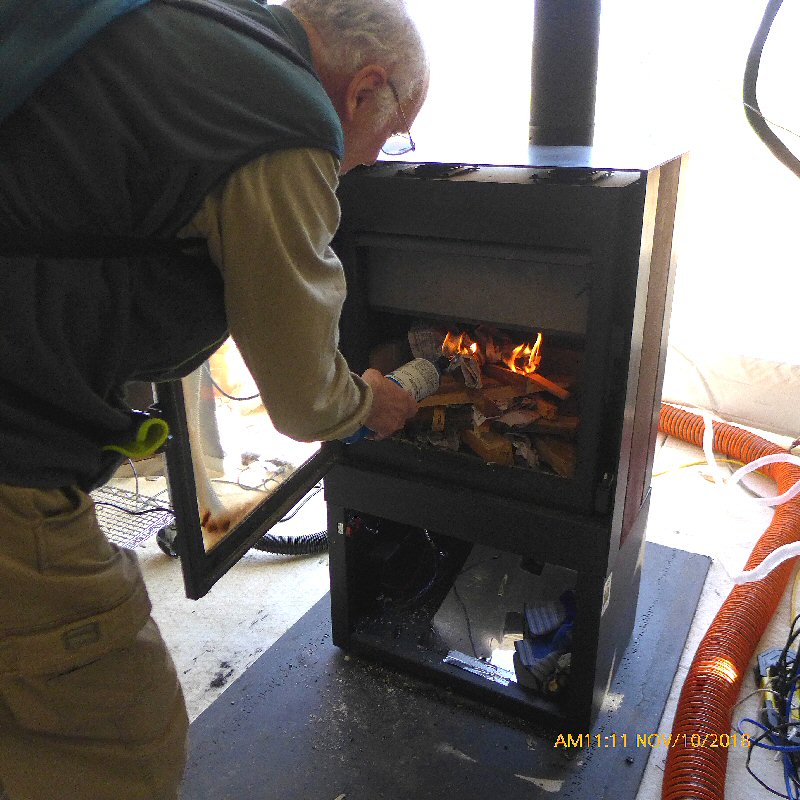
Automated stoves judge Mark Knaebe lights the SBI fireplace stove for a
testing run.
Mark is a United States Forest Service scientist at the Forest Products
Research Laboratory in Madison, Wisconsin.
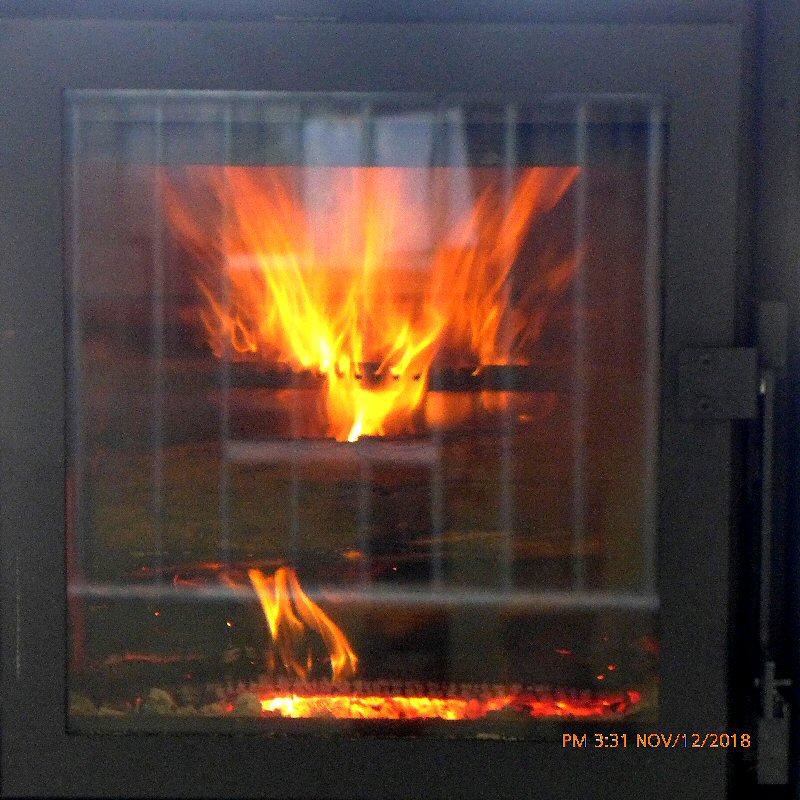
We
tested the stove simultaneously with Brookhaven for 1 run. However, on
the Saturday morning it was super windy. The Condar controller depends
on measuring chimney pressure accurately, and this was virtually
impossible due to large fluctuations. The PM number was 2X
the
BNL (Brookhaven) number. On two other runs with calmer weather, on the
Wittus and the VcV stoves, we had good agreement.
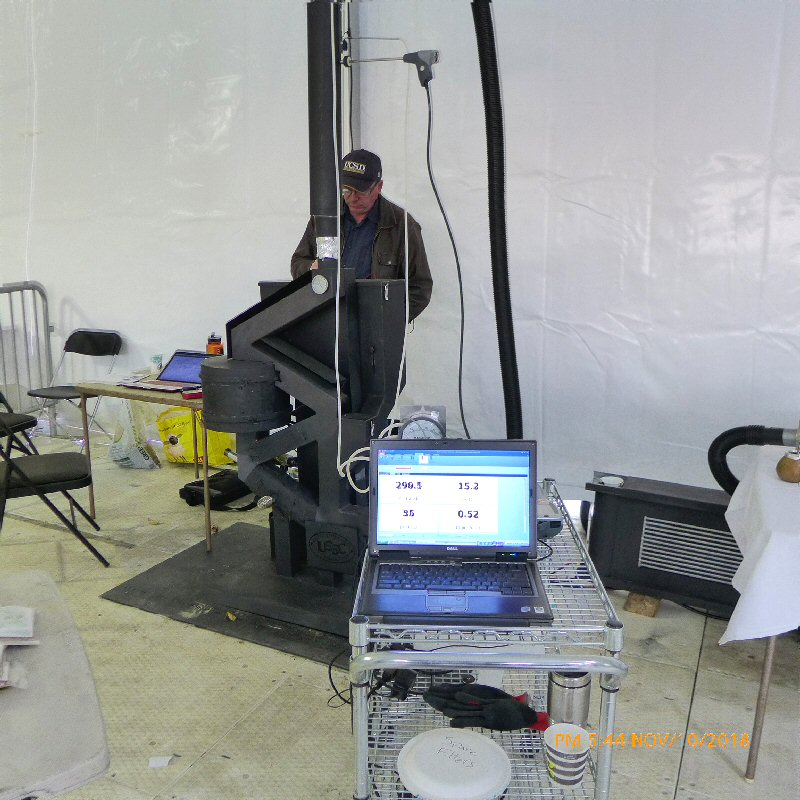
Thermoelectric expert Fred
Leavitt of Vulcan Energy used commercially available TEGs by
Hi-Z, and adapted the gravity feed Wiseway pellet stove
to get an output up to 130 watts. He won second place in the
thermoelectric category.
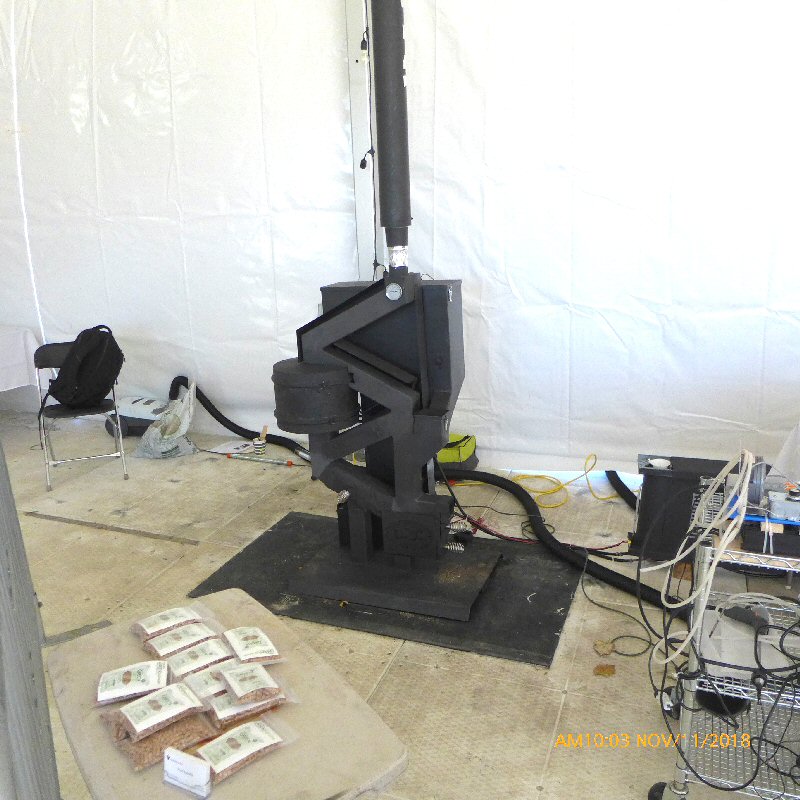
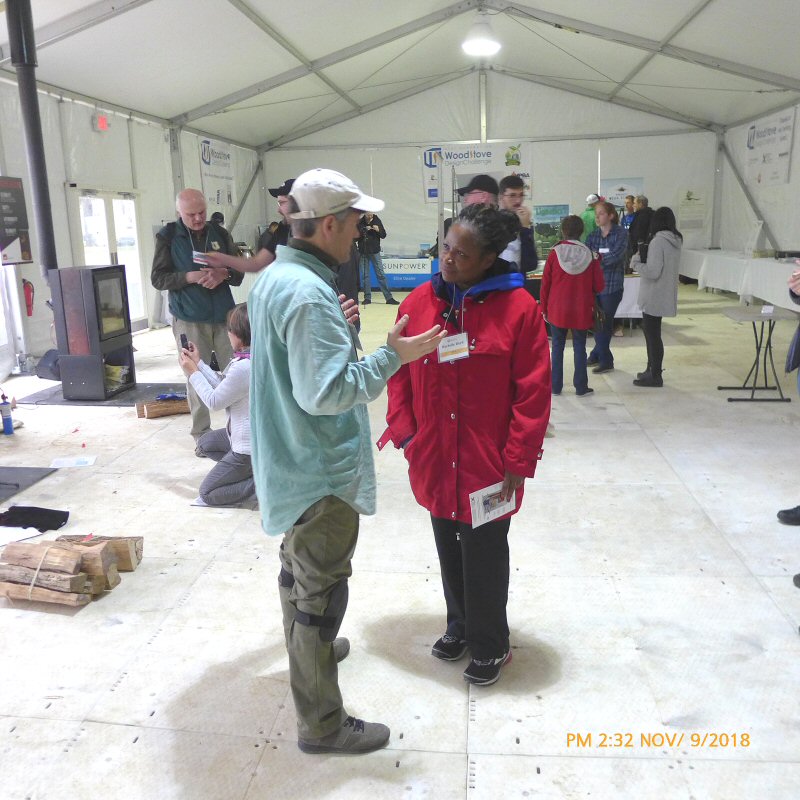
Tulikivi's North American head Boris Kukolj discusses masonry heaters
and the NSPS with EPA's Rochelle Boyd.
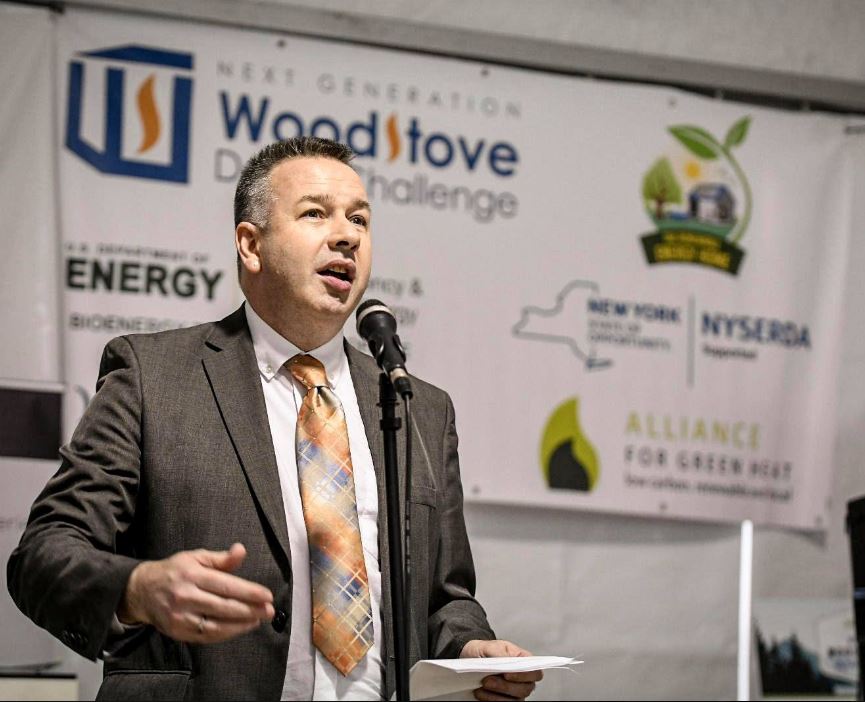
Jonathan
Male, head of U.S. Department of Energy's (DOE) Bioenergy Technologies
Office, and a lead sponsor of the Challenge, addressing the teams. DOE
was very pleased with the event. Alliance for Green Heat was able to
engage them to now include residential biomass heating in their
programmatic work.
Biomass is the second largest source of renewable energy in the United
States, ahead of solar and wind.
Domestic heating accounts for 25% of biomass use
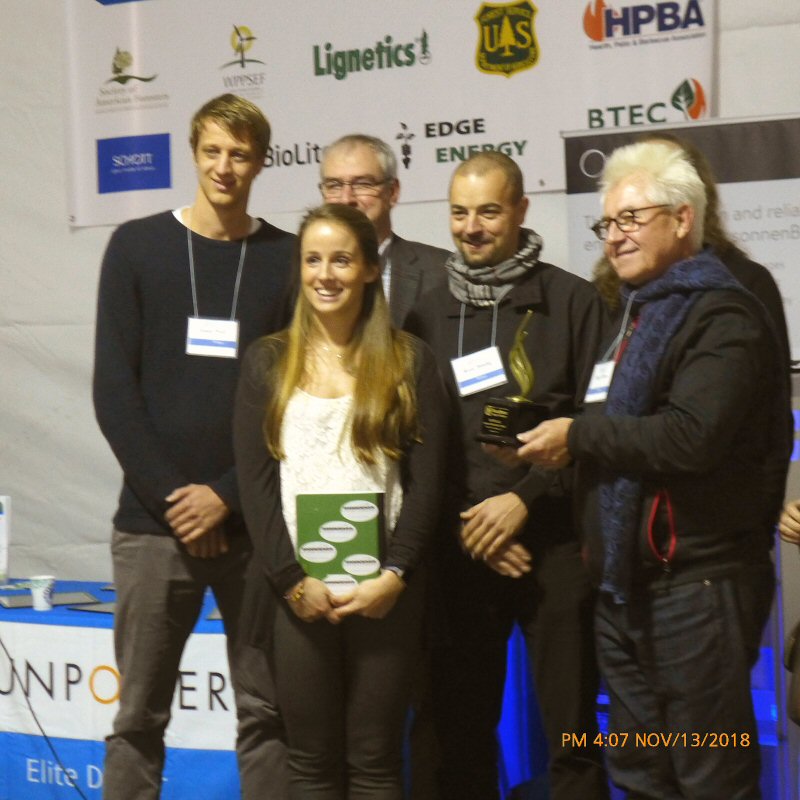
Rebecca Trojanowski from Brookhaven National Laboratory presented the
First Place award in both categories (automated and thermoelectric) to
the Wittus team, from Denmark and Germany.
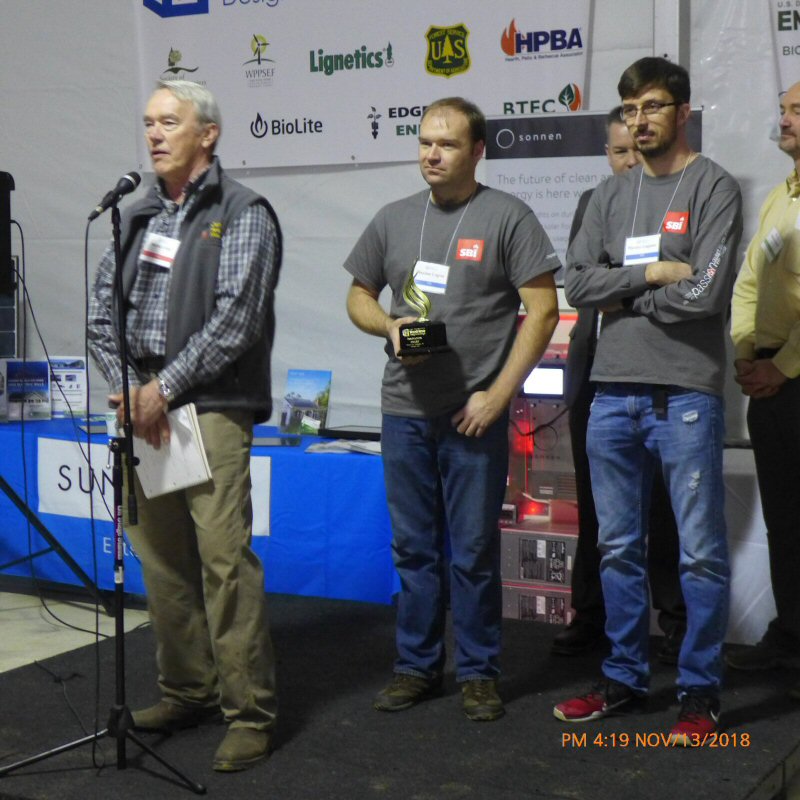
I had the pleasure of presenting the Innovation Award at
the closing ceremonies. It went to Stove Builders International (SBI) a
major Canadian Company based in Quebec. They showed a prototype
fireplace stove that was completely automated, based on 2 simple
sensors - flue temperature and door open/closed. A sophisticated logic
board regulates 2 air control motors to keep the stack temperature
constant and boost the fire on a cold start. Their stove also had the
best fire viewing of all the stoves in the event. It also won 2nd place
overall in the automated category.
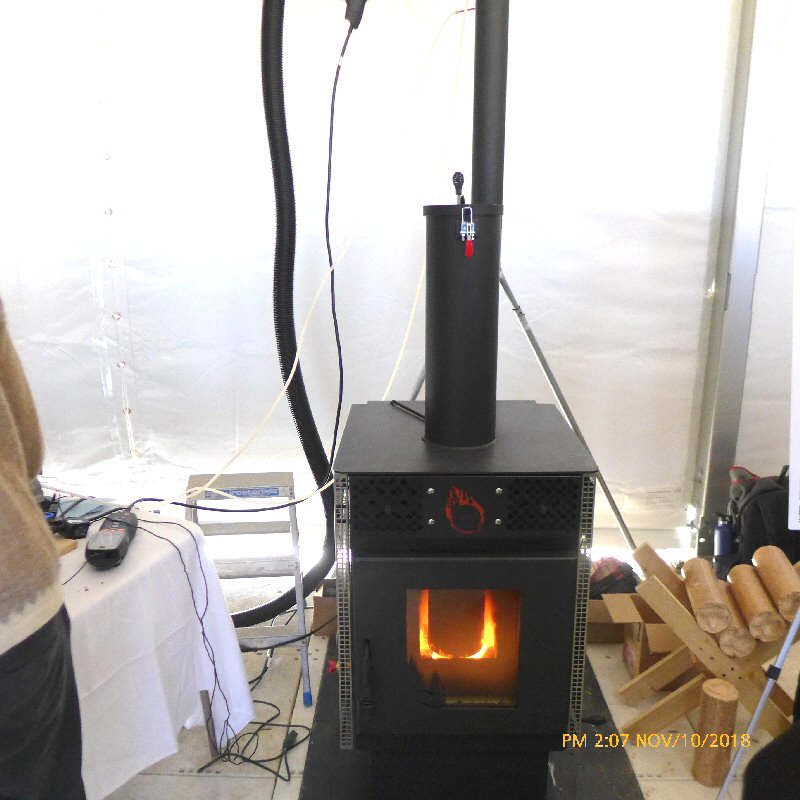
The "People's Choice" Award went to the 509Fab stove. It
features self feeding pressed logs, and has high efficiency and very
low PM and CO, see Condar summary below:
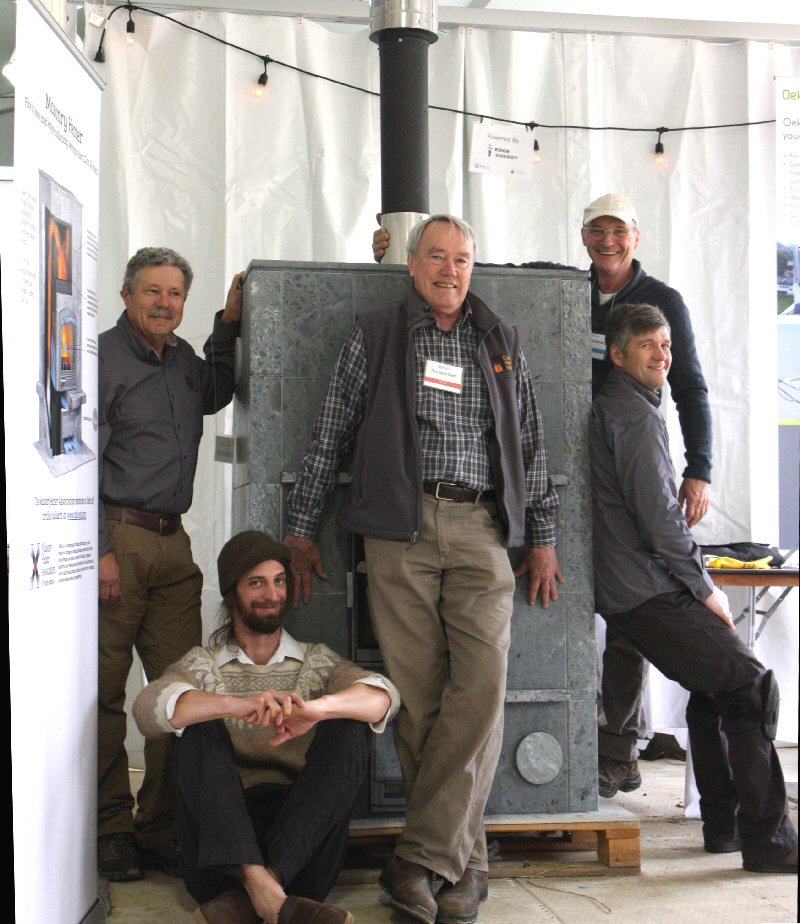
MHA Testing Team enjoying some stored heat.
Left to right: Ron Pihl, Jim Schalles, Norbert
Senf, Mark Seymour, Boris Kukolj.
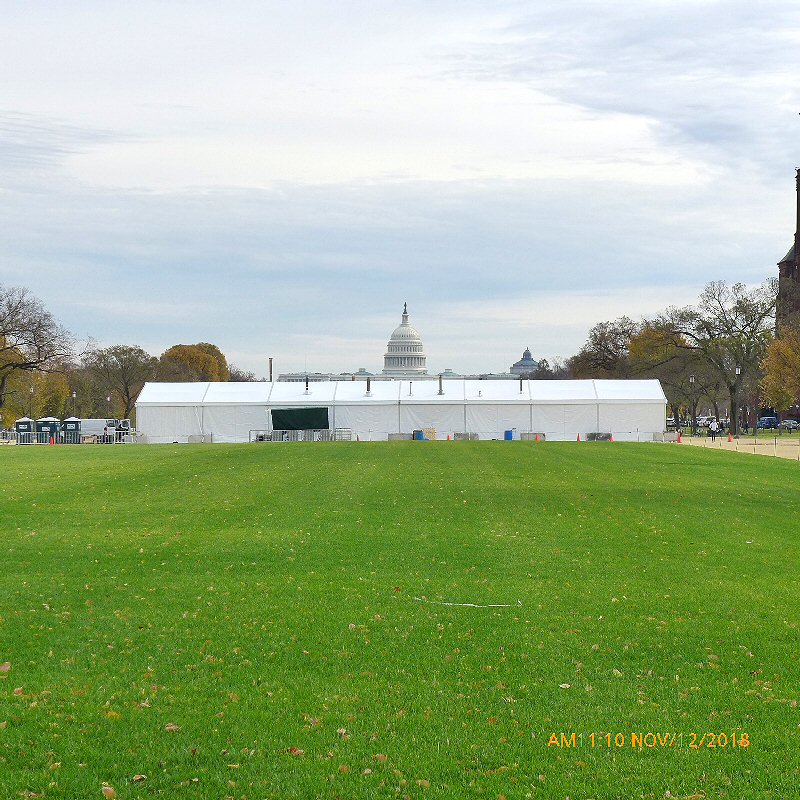
|